Controlled demolition is the systematic and planned dismantling or destruction of structures using specific techniques and equipment. It prioritizes safety, efficiency, and minimal environmental impact, often seen in urban areas or close quarters where precision is essential.
If you want to learn more about this demolition technique, read on.
What Is the Control Demolition Method?
Controlled demolition is much more than just “knocking things down.” It’s a meticulously orchestrated procedure where every step is calculated to ensure that buildings or structures are dismantled in the safest and most efficient manner possible.
This method stands in contrast to unplanned demolitions, which can be hazardous and inefficient. Controlled demolition factors in various considerations – from the structural integrity of the building to its surroundings, environmental implications, and the potential reusability of materials.
Applications and Use Cases
With its precision-based approach, controlled demolition has found applications in many scenarios.
Historical Buildings and Landmarks
- Preservation of Heritage: Controlled demolition allows for selective deconstruction, ensuring that historically significant portions of the building can be preserved or restored.
- Material Salvaging: Antique bricks, tiles, woodwork, or fixtures can be meticulously extracted for reuse or historical replications.
- Protecting Legacy: Given their age, these buildings might not comply with modern safety standards. Controlled demolition ensures these structures are treated safely, protecting the legacy they embody without risking present-day lives.
Urban Settings with Adjacent Structures
- Minimized Disruptions: Controlled demolition ensures the process is contained within a predefined boundary to avoid disruptions to adjacent buildings, roads, or public spaces.
- Safety First: The risk of collateral damage in such settings is high. Precision-based techniques ensure that adjacent structures remain unharmed.
- Traffic Management: Controlled demolition can be orchestrated in phases to ensure traffic, both vehicular and pedestrian, faces minimal disruptions.
Buildings with Structural Issues
- Risk Mitigation: Buildings with structural issues are like ticking time bombs. Controlled demolition ensures these are safely dismantled without accelerating potential collapses.
- Assessment Led: A comprehensive assessment identifies the weak points before any action is taken. This intelligence-driven approach ensures maximum safety.
- Emergency Responses: In some cases, such as after earthquakes, controlled demolition can be employed as a rapid response tool to safely bring down structures that pose threats.
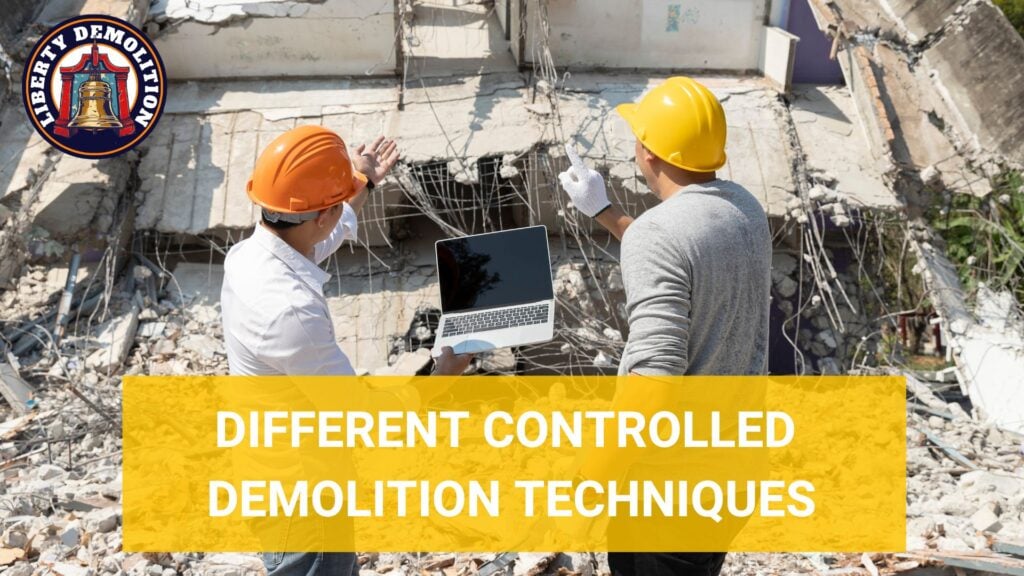
What are the Different Controlled Demolition Techniques?
Here are some of the most widely used controlled demolition techniques.
Implosion
It involves using explosives to swiftly bring down a structure. But contrary to what it might seem, it’s not about a massive explosion – it’s about strategic placement. Explosives are positioned at specific structural points, typically the building’s main supports. When detonated, these explosives cause the building to collapse inward, minimizing danger to surrounding areas.
High Reach Arm
This is a more modern technique and involves machinery that combines elements from excavators and demolition shears. A high-reach arm, sometimes extending over 150 feet, is used to tear down structures from the top down. This is often used for buildings taller than 20 meters. However, the size and weight of the machinery can limit its applicability, and it might be slower than implosion for very large structures.
Crane and Ball
An old but effective method, this technique uses a wrecking ball, often weighing up to 13,500 pounds, swung or dropped onto a structure. A crane operator uses momentum to swing the ball into the structure, breaking it apart.
Selective Demolition
Also known as deconstruction, this technique is more about disassembling than outright destruction. Structures are taken apart largely by hand or with minimal machinery, preserving valuable elements for reuse. While eco-friendly and sustainable, this technique is also labor-intensive and time-consuming.
Hydraulic Pusher
Hydraulic pushers apply a force to push over walls or sections of buildings and are used for structures made of brick or light concrete. Hydraulic rams are placed against a structure, applying steady pressure until it collapses. It’s controlled and effective for specific structures but is limited to certain types of buildings.
Controlled Demolition vs. Traditional Demolition
Demolition techniques can largely be divided into two categories: controlled and traditional. While the goal – to bring down a structure – remains constant, the methodologies and outcomes differ significantly.
Feature/Aspect | Controlled Demolition | Traditional Demolition |
Planning and Precision | Detailed planning and strategizing | General planning, more brute force approach |
Techniques and Tools Used | Specialized techniques (e.g., implosion) and advanced technologies | General-purpose machinery like bulldozers |
Time and Labor | More time in planning, faster actual demolition with specialized labor | Longer execution time, more manual labor |
Safety and Environmental Concerns | High safety standards, focus on environmental impact | Safety considered, but potential for higher risk |
Cost and Efficiency | Higher upfront costs but potential long-term savings due to efficiency | More cost-effective short-term, less resource recovery |
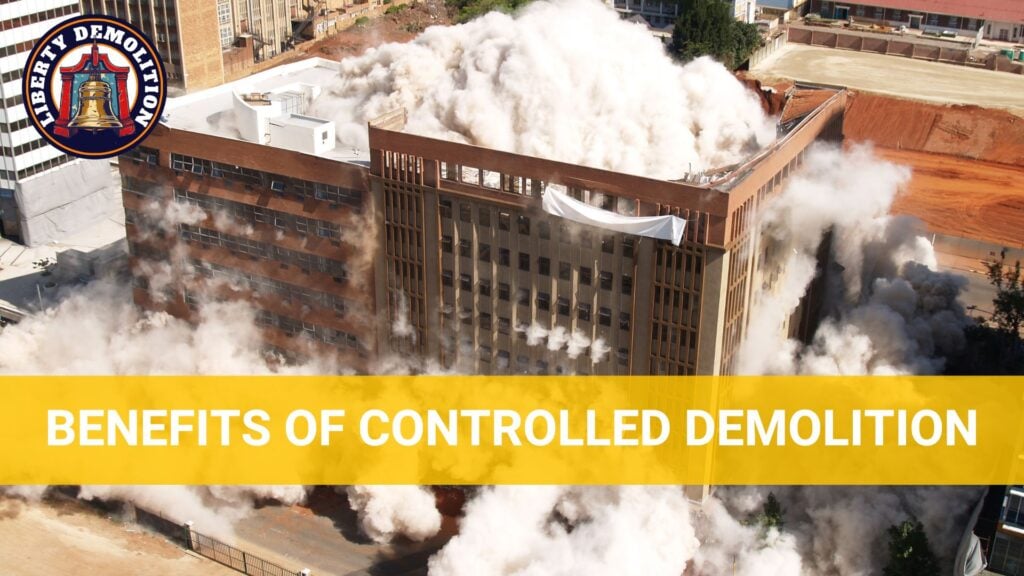
Controlled Demolition Guide: The Benefits
Here are the top reasons why controlled demolition is often the chosen method for modern structures:
1. Predictable Outcomes
The demolition is carefully planned to ensure that the building comes down in a very specific manner. This reduces the element of unpredictability, which commonly happens in traditional demolitions. At times, only a part of a structure needs to be demolished, perhaps to make way for renovations or extensions. With controlled demolition, it’s possible to target specific sections of a building without compromising the integrity of the rest.
2. Minimized Collateral Damage
Controlled demolition ensures that adjacent properties, infrastructure, and public areas are not inadvertently damaged. One of the significant issues with demolitions is the unpredictable scatter of debris. Controlled methods help contain this debris to make sure it falls within a predefined area, minimizing risks.
3. Enhanced Safety Protocols
Before any action is taken, a comprehensive risk assessment is conducted. This allows for the identification of potential hazards to make sure measures are in place to mitigate them. From using drones for aerial assessments to leveraging sophisticated software for simulations, controlled demolition leverages technology to enhance precision and accuracy.
4. Cost-Efficiency in the Long Run
The precision of controlled demolition often translates to fewer damages to surrounding structures or infrastructures, which translates to savings in potential repair or legal costs. With a precise demolition, it’s easier to salvage valuable materials from the site, which can be recycled or sold, offsetting some of the demolition costs.
5. Reduction in Unforeseen Hazards
Before initiating the demolition, comprehensive surveys and risk assessments identify and mitigate potential hazards, from structural weaknesses to the presence of hazardous materials like asbestos. Controlled demolition often involves expert demolition contractors, specifically in risk management and hazard mitigation, ensuring a higher level of on-site safety.
6. Waste Reduction and Reduced Pollution
The precision of controlled demolition allows for a higher percentage of materials to be salvaged and reused. This can range from bricks and beams to doors and window frames. Moreover, controlled demolitions often use systems that reduce the dust released into the atmosphere, which can harm the environment and human health.
Pre-Demolition Steps
Every meticulously executed controlled demolition starts long before the first piece of machinery touches the building. These foundational processes ensure that when the demolition occurs, it’s seamless, safe, and as efficient as possible.
Comprehensive Site Analysis
- Structural Survey: This involves assessing the structure’s overall integrity, identifying load-bearing walls, and pinpointing potential hazards.
- Hazardous Material Assessment: Older buildings, in particular, might house materials like asbestos, lead, or other hazardous substances.
- Utility Mapping: Before initiating demolition, it’s essential to know where utility lines run – this includes gas, water, electricity, and telecommunication lines.
- Environmental Considerations: How will the demolition affect the local environment? Issues like potential water runoff, dust creation, or impact on nearby flora and fauna need to be considered and planned for.
- Neighborhood Impact Study: In urban settings or densely populated areas, understanding how the demolition will affect daily life is crucial. This might involve traffic assessments, noise level predictions, or even understanding how shadow or light patterns might change post-demolition.
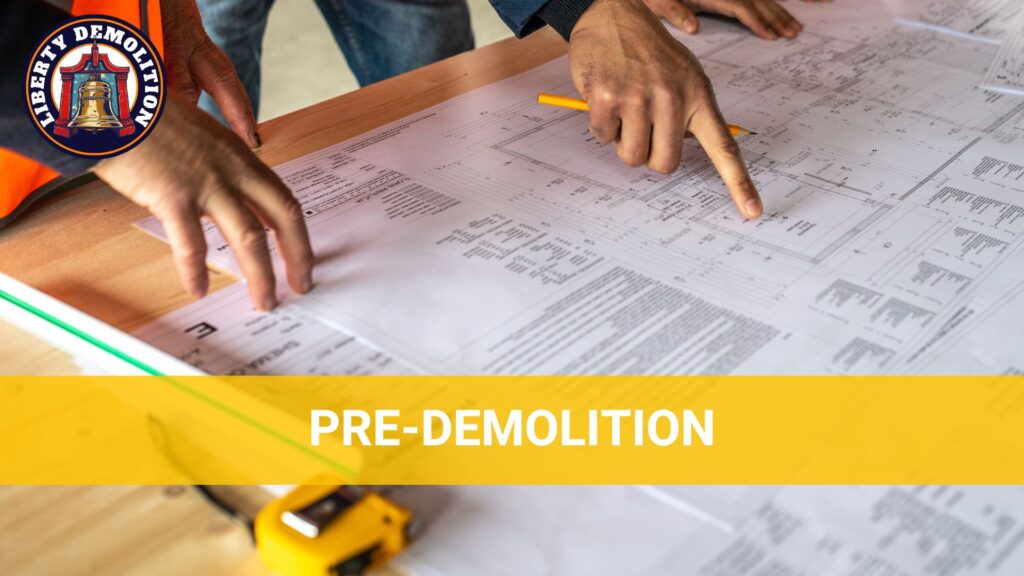
Obtaining Necessary Permits and Approvals
- Local Authority Permissions: Most local governing bodies have a set of regulations and guidelines for demolitions.
- Environmental Clearances: These are required, especially if hazardous materials are involved, or the site is near sensitive ecological zones.
- Heritage and Cultural Approvals: Additional permissions might be required if the building or site holds historical or cultural significance.
- Stakeholder Communication: This includes informing neighboring properties, local businesses, and the general public about the upcoming demolition, its timeline, and any potential disruptions they might experience.
- Emergency Services Coordination: In some areas, it might be required to inform and coordinate with local emergency services to prepare them for any unforeseen situations so they can respond promptly if required.
Preparing the Site
In controlled demolition, preparing the site is a combined planning of logistics, safety, and strategy.
Evacuation Procedures
- Resident and Tenant Coordination: For inhabited structures, it’s essential to ensure that everyone vacates well before the demolition begins.
- Temporary Relocation Assistance: In some cases, residents or businesses might need assistance in relocating temporarily.
- Safety Briefings: Those living or working nearby should be informed about the demolition and given guidelines on what to expect and how to stay safe, especially if there’s a risk of flying debris or loud noises.
Barrier Setup and Site Containment
- Physical Barriers: Erecting fences, hoardings, or other barriers helps keep unauthorized personnel out and ensures that debris remains contained within the site.
- Noise and Dust Control: Sound barriers can be set up to minimize the noise impact on the surrounding areas. Similarly, water mist systems or tarpaulins might be employed to control dust dispersion.
- Traffic Diversions: Especially in busy urban settings, it might be necessary to divert traffic, both vehicular and pedestrian, away from the site.
Utility Disconnections and Rerouting
- Cutting off Utilities: Before the first hammer falls, all utilities connected to the structure – electricity, water, gas, and telecommunications – must be disconnected to prevent accidents and disruptions.
- Rerouting Services: In cases where the building’s utilities serve nearby structures or areas, provisions might need to be made to reroute these services temporarily.
Salvage and Material Management
- Salvaging Valuables: Before the demolition begins, valuable or reusable items, such as architectural details, fixtures, or even recyclable materials, are identified and removed.
- Hazardous Material Handling: If the site survey identified potentially hazardous materials like asbestos, these would be safely removed and disposed of following regulatory guidelines.
Equipment and Personnel Staging
- Machinery Placement: The heavy machinery required for the demolition, such as excavators, bulldozers, or cranes, is positioned strategically, ensuring optimal access and maneuverability.
- Safety Equipment: It’s crucial to set up safety equipment, from helmets and protective gear for the personnel to fire extinguishers and first aid stations.
- Crew Briefings: Every individual on the site, from the machine operators to the site supervisors, should be briefed on the day’s plan, safety protocols, and emergency response procedures.
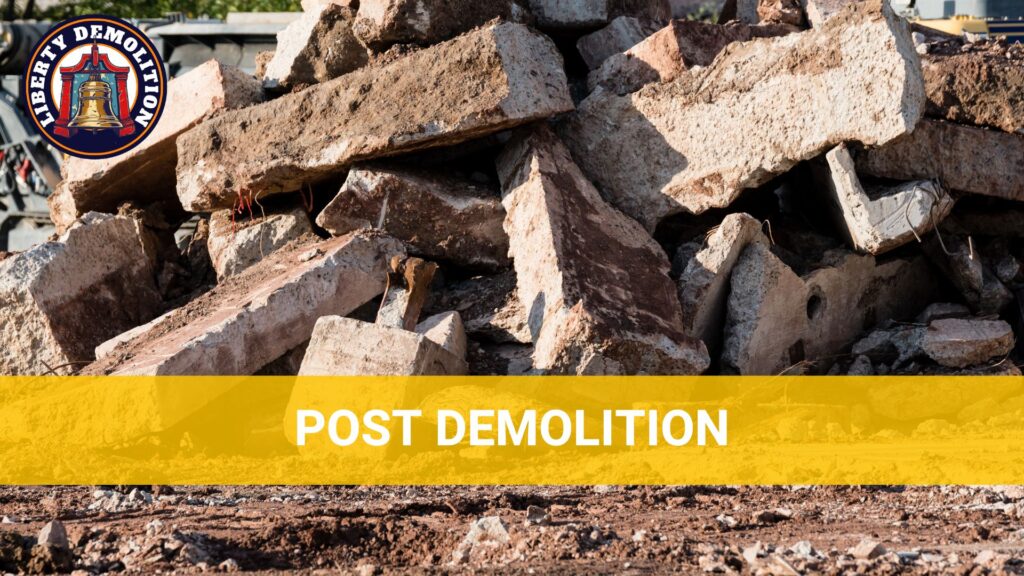
Post-Demolition Activities
Among the most crucial post-demolition tasks is managing the mountain of waste and debris left behind.
Waste and Debris Management
1. Segregation of Waste
- Sorting at Source: As the structure is brought down, materials are sorted based on type – concrete, metal, wood, glass, and so forth.
- Hazardous Waste Identification: Any hazardous materials, such as asbestos or lead-based items, are separated.
2. Recycling and Reusing Materials
- Metal Salvaging: Metals like steel, copper, and aluminum can be sent to recycling facilities.
- Concrete Recycling: Concrete can be crushed and reused as aggregate for new construction projects or as a base for roads and pavements.
- Reclaiming Wood: Wooden beams, planks, or fixtures can either be reused directly in other constructions or sent to facilities that can transform them into engineered wood products.
3. Safe Disposal of Waste
- Landfill Deposits: Non-recyclable materials are dispatched to designated landfills.
- Special Handling for Hazardous Waste: Materials like asbestos or certain chemicals require specialized disposal methods. These are often handled by certified professionals who ensure their disposal meets environmental and safety standards.
3. Site Cleanup and Restoration
- Dust Management: Doing water sprays or other dust suppression methods ensures the area is safe for workers and nearby residents.
- Ground Leveling: With the debris cleared, heavy machinery is often used to level the ground to prepare it for the next phase, be it construction or landscaping.
- Soil Testing: If a new construction is planned, soil tests might be conducted to ensure it’s suitable for the intended purpose.
4. Documentation and Reporting
- Waste Disposal Records: It’s essential to maintain records of where and how waste was disposed of, especially if hazardous materials were involved.
- Environmental Impact Reporting: In some jurisdictions’ post-demolition, there might be a need to document and report the environmental impact of the process.
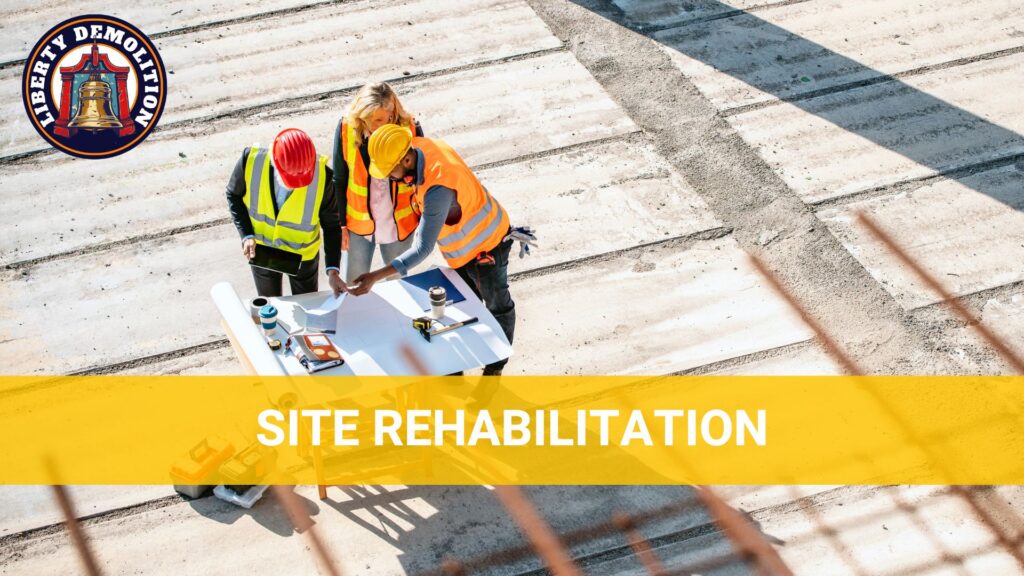
Site Rehabilitation and Future Planning
Site rehabilitation involves restoring the land to a usable state while envisioning its future potential.
1. Soil Restoration and Stabilization
- Removing Contaminants: Any leftover hazardous materials or contaminants need to be identified and safely removed to ensure the soil is healthy.
- Erosion Control: Implementing measures like silt fences or erosion control blankets can help stabilize the soil and prevent erosion.
2. Green Initiatives
- Revegetation: Planting trees, shrubs, or grass can help restore the natural ecosystem and improve the site’s aesthetics.
- Creating Green Spaces: Depending on the future plans for the site, it might be transformed into a park, community garden, or other green spaces for public use.
3. Future Development Planning
- Assessing Potential: With the site cleared, stakeholders can conduct a comprehensive analysis to determine its best potential use, whether residential, commercial, or mixed-use.
- Engaging with the Community: Before moving ahead with development plans, it’s wise to engage with the local community, gathering input and ensuring that the site’s future aligns with the broader needs and wishes of the area.
- Infrastructure Setup: Depending on the future use, it might be necessary to lay down infrastructure like roads, sewage systems, or utilities.
Plan Ahead, Do It Right
Controlled demolition is more than just tearing down buildings. It’s about planning, precision, safety, and thinking about the future. Every step, from the initial planning to the cleanup, matters.
When considering a demolition project, it’s important to work with professional demolition contractors who understand the importance of doing it right. Professionals who prioritize safety, are committed to recycling and reusing materials, and ensure a clean site ready for the next chapter.
Thinking about a demolition project? Choosing a team that brings experience, skill, and a commitment to the environment is essential. For a reliable, eco-friendly, and comprehensive demolition solution, Liberty Demolition is here to help. Let’s build a better tomorrow, starting with today’s demolition.