A pavement breaker is a powerful tool used to break up hard surfaces like asphalt, concrete, and compacted soil. Its primary purpose is to assist in demolition, construction, and road repair projects.
To understand more about its functionalities and how it has become an essential tool in the construction industry, continue reading.
Pavement Breaker – Meaning and Uses
A pavement breaker is a heavyweight tool, both in terms of its physical weight and the force it delivers. They are essential equipment for many tasks in the construction sector. For many of us, the image that comes to mind is a worker wearing protective gear, using this tool to drill into the street. But there’s more to it:
- Functionality: The core function of a pavement breaker is to break hard surfaces. It can be used on various materials, such as asphalt, concrete, or even rocky terrains.
- Components: A pavement breaker comprises a chisel to break the surface and a motor to drive the chisel. The motor can be driven by air (pneumatic), electricity, or hydraulic power. The choice depends on the specific requirements of the job.
- Applications: While it’s commonly associated with road work, pavement breakers are also used in other sectors. They’re often spotted in demolition sites, breaking down walls or floors. Mining industries also employ them to break rocks.
Components of a Pavement Breaker
Here’s a look at what makes a pavement breaker a power tool:
1. The Power Source
The power source is what drives a pavement breaker to deliver its immense force. Depending on the model and its intended use, a pavement breaker can be powered by one of three main sources: pneumatic, hydraulic, or electric.
Pneumatic (Air-powered)
Pneumatic pavement breakers operate using compressed air. An external air compressor feeds the tool with pressurized air, which powers a piston inside. This piston moves rapidly back and forth, which pushes the chisel into the surface with a repeating, powerful force.
Pneumatic breakers are often preferred for heavy-duty tasks due to their high power output. They are durable, require less maintenance, and are typically lighter than their hydraulic or electric counterparts. You’ll see them mostly in large-scale construction sites, roadworks, and demolition jobs.
Hydraulic (Fluid-powered)
Hydraulic pavement breakers use fluid to transfer power. A hydraulic pump, often externally connected, pushes hydraulic fluid into the tool. This action powers a hydraulic motor inside, which then drives the chisel.
These breakers offer a consistent power output, which makes them suitable for prolonged tasks. They are also less sensitive to environmental conditions like dust or moisture. Hydraulic pavement breakers are common in underground construction and mining operations due to their resilience in challenging environments.
Electric (Battery or Cord-powered)
Electric pavement breakers use an electric motor, which can be powered either by plugging the tool into an outlet or using a battery. The motor drives a set of gears that move the chisel.
These are often lighter and more mobile due to the lack of external power connections. They’re cleaner in operation, producing no emissions, and are quieter than pneumatic or hydraulic versions. Electric pavement breakers are ideal for smaller tasks, indoor jobs, or areas where the noise or emissions of other types would be problematic.
2. The Chisel or Bit: Types and Uses
The chisel, often referred to as the “bit,” is the point of action for any pavement breaker. This is the part that comes into direct contact with the material being worked on.
Flat Chisel
This chisel has a flat end. It’s one of the most common types you’ll see in a pavement breaker. Flat chisels are versatile and are used for general breaking and chipping tasks. They’re ideal for breaking up flat surfaces like roads and pavements.
Pointed Chisel
This type has a sharp, pointed end. The design focuses the energy of the pavement breaker onto a small area and ensures deeper penetration. Pointed chisels are used when precision is required, such as creating starting points for cracks or breaking through very tough materials. They’re commonly employed in demolition tasks that aim to pierce through concrete or stone quickly.
Spade Chisel
This chisel has a broader, flatter blade, somewhat resembling a spade or shovel. It’s used for digging and cutting through materials like asphalt or clay. In construction, it’s often employed to dig trenches or channels in the ground.
Bushing Chisel
This chisel has multiple serrated points. It looks somewhat like a comb and covers a larger surface area than most other chisels. Bushing chisels are used to roughen up surfaces. If you’re preparing a concrete floor for tiling, for instance, using a bushing chisel can help create a rough texture to ensure better adhesion of tiles.
Asphalt Cutter
This chisel is long with a sharper, more rectangular blade. It’s specifically designed to cut through asphalt. It provides a cleaner cut than standard flat or pointed chisels.
Flex Chisel
This more flexible, thinner chisel allows for slight bends and adjustments. Flex chisels are employed when removing tiles or thin layers of material from surfaces. They can get under the material and pop it off with ease.
3. Trigger System and Ergonomic Handle
The interface between the user and the pavement breaker is crucial for both efficiency and safety. Two key elements in this interface are the trigger system and the handle.
Trigger System
The trigger system is what allows the operator to control the tool’s power and operation. It is essentially the on-off switch but may come with more advanced functionalities in modern breakers.
Types of Triggers:
- Simple On/Off: The most basic type; it activates the tool when pressed and stops it when released.
- Variable Speed: This allows the operator to adjust the power output. By pressing harder or softer on the trigger, the tool can run faster or slower.
- Lock-On: Some pavement breakers come with a lock-on feature, which keeps the tool running without having to continuously press the trigger. This can be beneficial for extended tasks but must be used with caution to ensure safety.
- Safety Aspects: Many modern pavement breakers incorporate safety mechanisms into their triggers, such as a double-trigger system to prevent accidental activation. Others might have a quick shut-off feature to stop the tool rapidly in emergencies.
Ergonomic Handle
Given the heavy-duty nature of pavement breakers, having an ergonomic handle is essential. This design aspect ensures that the tool can be used for extended periods without causing undue strain or injury to the operator.
Design Features:
- Vibration Dampening: One of the significant issues with pavement breakers is the vibration they produce. Excessive vibration can lead to conditions like Hand-Arm Vibration Syndrome (HAVS). Modern handles often have systems in place to dampen or reduce this vibration, protecting the user.
- Multiple Gripping Points: Some breakers come with more than one handle, allowing the user to grip the tool in different ways and distribute the weight and force more evenly.
- Material and Grip: The handle’s material can make a difference. Soft-grip materials can provide better hold and reduce the strain on the hands. Additionally, materials that resist slipping when wet can be beneficial in certain conditions.
- Adjustability: Depending on the tool and brand, some handles are adjustable. This allows operators of different sizes and preferences to modify the tool’s grip to their liking, offering a more personalized and comfortable experience.
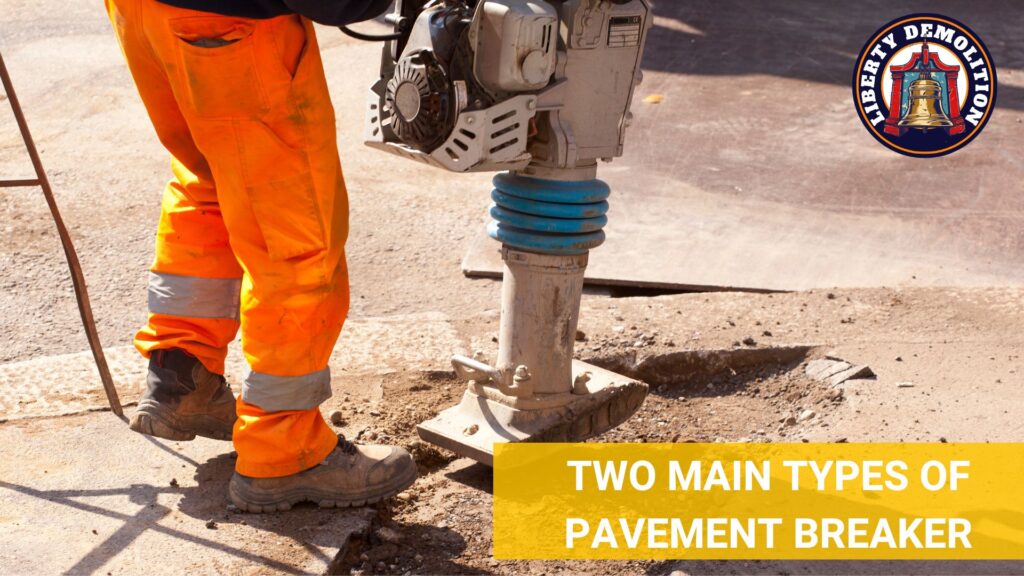
What Are the 2 Main Types of Pavement Breakers?
Pavement breakers can be broadly categorized based on several criteria: power source, size, and function. However, when looking at the primary distinction in size and function, the two main types that stand out are heavy-duty pavement breakers and light-duty pavement breakers.
Heavy-Duty Pavement Breakers
They are generally heavier, often weighing over 60 pounds, sometimes even more. These tools deliver higher power outputs, capable of breaking through dense materials like reinforced concrete and hard rocks. The overall size of heavy-duty breakers is larger, which allows for more significant force distribution and deeper penetration.
Applications:
- Infrastructure Development: Heavy-duty breakers are typically used in large-scale projects like highway construction, bridge demolitions, and major city roadworks.
- Mining: Their ability to penetrate hard rock surfaces makes them invaluable in mining operations.
- Major Demolitions: When tearing down buildings or large structures, these breakers play a pivotal role in breaking through thick walls and foundations.
- Power Source: Given their high-power requirements, they are often pneumatic or hydraulic, although there are electric models available that can deliver comparable power.
Light-Duty Pavement Breakers
Light-duty breakers, while not as powerful as their heavy-duty counterparts, offer versatility and are more suitable for precision tasks and smaller projects. These are relatively lightweight, often weighing between 20 to 50 pounds, which makes them more portable and easier to handle.
They provide enough power to handle tasks like breaking tiles, thin layers of concrete, and asphalt but might struggle with thicker, more reinforced materials. Being compact, they are more maneuverable, which allows better precision in tighter spaces.
Applications:
- Residential Construction: They are commonly used in home renovations, breaking up old driveways, or making modifications to residential properties.
- Plumbing and Electrical Installations: Light-duty breakers are the go-to tools when channels or holes need to be created in walls or floors for plumbing or wiring.
- Landscaping: They can also be used in landscaping projects, breaking up small concrete paths or creating spaces for water features.
- Power Source: Many light-duty pavement breakers are electric, given their portability and the convenience of not needing external compressors or hydraulic setups. However, pneumatic and hydraulic models are also available for specific applications.
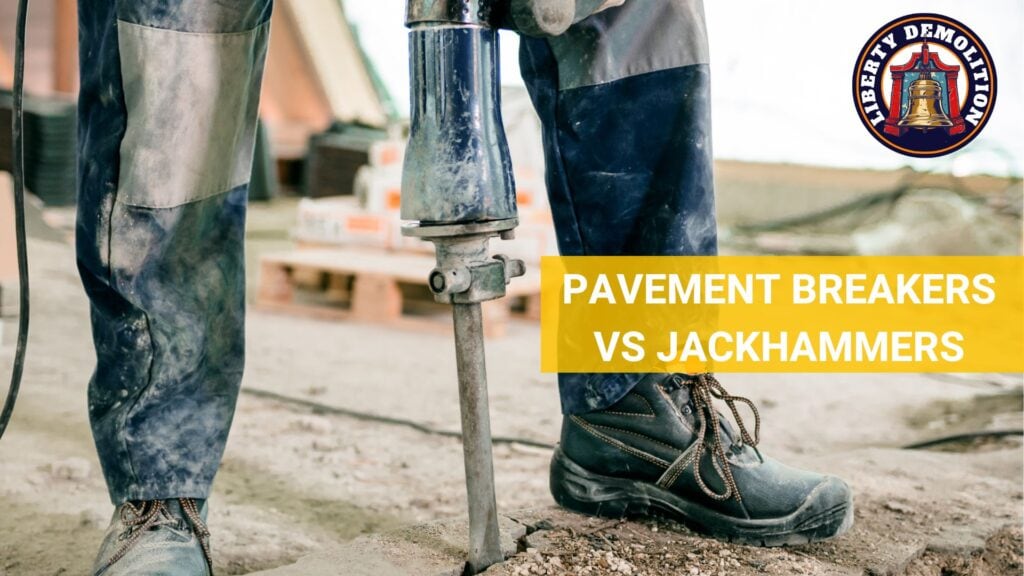
What Are the Differences Between Pavement Breakers and Jackhammers?
The terms “pavement breaker” and “jackhammer” are often used interchangeably, which leads to some confusion. While they share similarities, there are distinctions between the two tools.
Here’s a concise table highlighting the differences between pavement breakers and jackhammers:
Criteria | Pavement Breaker | Jackhammer |
Basic Definition | Designed specifically to break up hard surfaces like asphalt and concrete. | General term for a pneumatic drill or hammer used to break up various surfaces. |
Design & Orientation | Optimized for horizontal work on flat surfaces like roads. | Primarily designed for vertical operations but can work horizontally. |
Applications | Mainly used for road construction, maintenance, and repair. | Versatile; used for roads, demolition, trenches, and mining. |
Power Source | Can be pneumatic, hydraulic, or electric. | Traditionally pneumatic but also available in hydraulic and electric variants. |
Size & Weight | Generally bulkier and heavier. | Ranges from heavy models to lighter, more portable options. |
Terminology | More common within specific construction sectors. | Widely recognized term by the general public and broader in application. |
What Are the Uses of Pavement Breakers?
Their primary function revolves around breaking hard surfaces, but they have a variety of specific applications tailored to their design and power source.
Breaking Asphalt for Road Repair
Roads, especially asphalt ones, are subjected to a lot of wear and tear due to traffic, environmental factors, and time. Over the years, they develop cracks, potholes, and other forms of damage that need to be addressed to ensure safe driving conditions.
Pavement breakers are used to break and remove damaged sections of asphalt. Their high power output can rapidly break through asphalt layers, speeding up the repair process. The choice of chisel or bit can allow workers to target specific damaged areas without affecting the surrounding, intact sections of the road.
Concrete Slab and Foundation Removal
Given the density and strength of concrete, especially in foundations, pavement breakers offer the necessary force to break them apart. Using a pavement breaker allows for a controlled demolition, which minimizes the risk of unintended structural damage or injuries. With different chisels or bits, workers can switch between chipping away large chunks or delicately navigating around utilities and reinforcements.
Trenching and Other Utility Work
Trenches need to be dug in urban environments to install utilities like water pipes, gas lines, or electrical conduits. These trenches often pass through roads, pavements, or other hard surfaces.
Pavement breakers are used to break the surface layer, whether asphalt, concrete, or compacted soil, to facilitate trenching. By controlling the force and using specific chisels, workers can ensure trenches are of the required depth and width. Post utility installation, the trenches are filled, and the surface is restored. Pavement breakers play a role in ensuring the surface is adequately compacted and leveled, ready for the final layer.
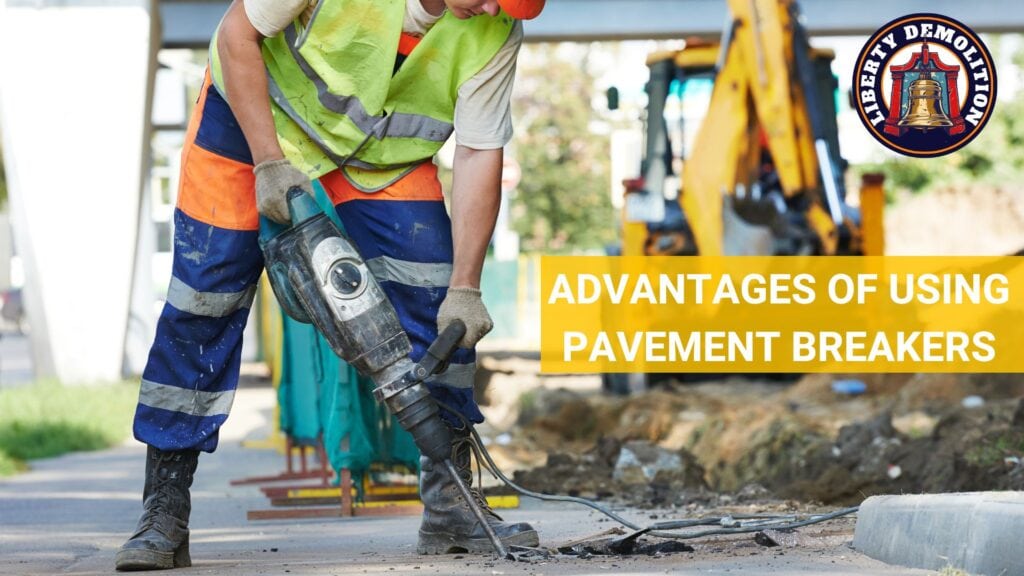
Advantages of Using Pavement Breakers
While the immediate image may be of breaking roads, their benefits extend far beyond:
Efficient Breaking of Hard Surfaces
- Deep Penetration: Due to their design and power output, pavement breakers can penetrate deep into tough materials like concrete, asphalt, and compacted soil.
- Consistency: Unlike manual methods, pavement breakers deliver a consistent force, which ensures uniform breaking without leaving unworked patches.
- Minimized Damage: Their targeted force means the surrounding areas remain largely unaffected.
Time-Saving and Labor Reduction
- Speed: The sheer power of pavement breakers allows tasks to be completed much faster than manual methods or lesser-powered tools.
- Labor Efficiency: Using pavement breakers significantly reduces the number of laborers required for breaking tasks. A single operator can achieve what might take several workers to accomplish manually.
- Reduced Fatigue: Manual breaking methods can be exhausting. The mechanized power of pavement breakers ensures that workers don’t tire out quickly.
Versatility: From Roads to Runways
- Broad Application Range: While the primary use might be in road construction and repair, pavement breakers are versatile enough to be used in various scenarios.
- Airport Maintenance: Runways, made of thick concrete slabs, require regular maintenance. Pavement breakers play an important role in repairing and renovating these critical infrastructures.
- Varied Terrains: Whether it’s a city road, a remote construction site, a backyard renovation, or an expansive airport runway, pavement breakers can adapt and deliver.
- Multiple Power Options: With pneumatic, hydraulic, and electric variants available, there’s a pavement breaker for every scenario, be it indoors, in dense urban settings, or at expansive outdoor sites.
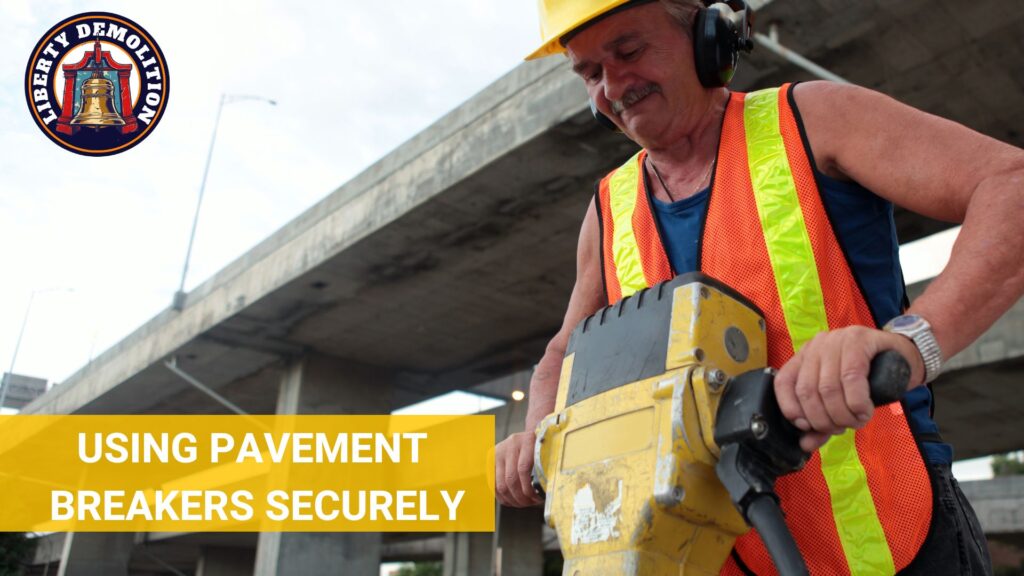
Using Pavement Breakers Securely
Ensuring secure and safe operation not only protects the user but also ensures the longevity of the equipment and the quality of the work:
Essential Protective Gear
- Ear Protection: Pavement breakers produce significant noise when in operation. Earplugs or earmuffs are essential to dampen this noise and safeguard the user’s hearing.
- Safety Goggles: During the breaking process, shards, splinters, and dust are inevitable. Safety goggles ensure that none of these particles can enter the eyes.
- Gloves: Handling a vibrating and forceful machine can be strenuous on the hands. Heavy-duty gloves not only offer protection against flying debris but also reduce the strain on the hands and fingers.
- Dust Masks (in certain conditions): When working in areas with a lot of fine dust or breaking materials that might release harmful particles, using a dust mask can protect the respiratory system.
Pre-use Inspection and Maintenance Checks
Before the pavement breaker is put to use, certain checks are vital to ensure both the tool’s safety and efficiency:
- General Inspection: Start with a visual inspection of the tool. Check for any visible damages, cracks, or signs of excessive wear.
- Chisel or Bit Inspection: Ensure that the chisel or bit is sharp and free of cracks.
- Connection Checks: For pneumatic or hydraulic pavement breakers, ensure that all connections are secure and free of leaks. This includes hoses, valves, and connectors.
- Vibration Dampening Systems: If the pavement breaker comes equipped with a vibration dampening system, ensure it’s functioning correctly.
- Trigger Mechanism: Test the trigger to ensure it operates smoothly. Any sticking or malfunctioning triggers should be addressed immediately.
- Regular Maintenance: Beyond pre-use checks, it’s essential to have a regular maintenance schedule. This includes cleaning, lubricating, and replacing worn-out parts.
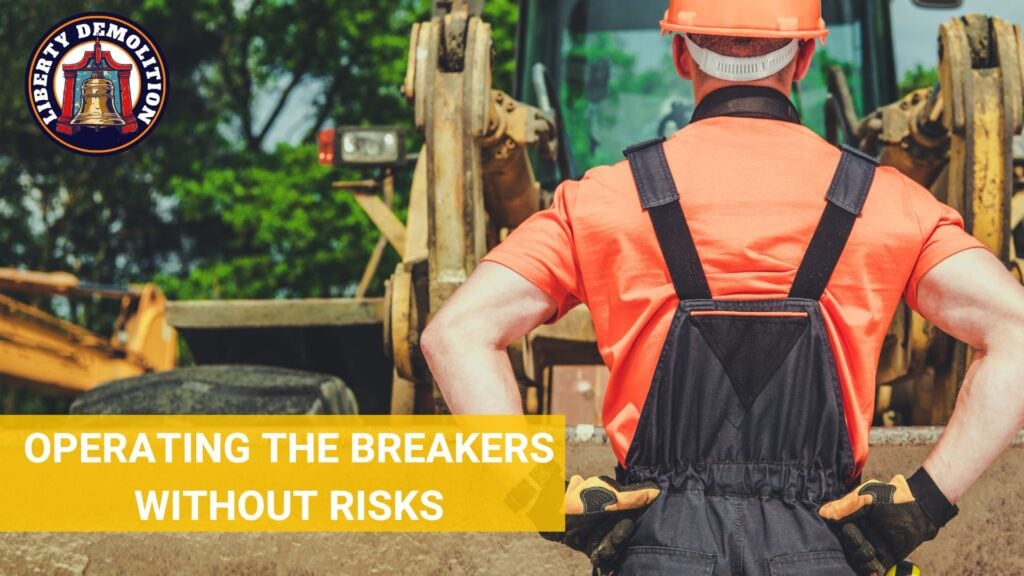
Operating the Breaker Without Risks
Operating a pavement breaker comes with inherent risks due to the tool’s power and the nature of its work. Here’s a list of tips on how to minimize the risks:
Proper Stance and Grip
- Stance: Maintaining a balanced and stable stance is crucial. The operator should stand with feet shoulder-width apart.
- Grip: Firmly grip the handles and make sure that the tool is under control at all times. Use both hands to distribute the weight and force evenly for breakers with dual handles.
Start Slowly
When activating the breaker, it’s advisable to start slowly to gauge the tool’s force and the surface’s resistance. This gradual approach helps prevent unexpected jerks or movements that can lead to accidents.
Beware of Buried Utilities
Before breaking any surface, especially in urban areas or established sites, ensure you have information about buried utilities like water pipes, gas lines, or electrical conduits. Striking one of these can lead to serious accidents.
Use Intermittently
Continuous operation can not only tire out the operator but also overheat the tool. Using the breaker in intervals, with regular breaks, ensures both the user and the equipment remain in optimal condition.
Stay Alert to Vibrations
Excessive or changed vibrations can indicate issues. It could be a sign of a malfunctioning tool or hitting a particularly hard or dense object.
Work in Well-Ventilated Areas
When working indoors or in confined spaces, ensure adequate ventilation. The dust and particles produced during the breaking process can be harmful when inhaled in large quantities.
Maintain Safe Distances
Ensure that bystanders, especially non-workers, maintain a safe distance from the operation area. The debris from the breaking process can fly out and pose a risk to those nearby.
Regular Breaks
Given the physically demanding nature of operating a pavement breaker, operators should take regular breaks. This helps reduce fatigue, minimizes the risk of hand-arm vibration syndrome, and keeps the operator alert.
Switch Off When Not in Use
Never leave the breaker running unattended. Even if stepping away for a short duration, switch off the tool to prevent any unintended activation or mishaps.
Stay Hydrated and Take Care of Health
Operating heavy machinery can be physically taxing. Drink water, use sunscreen if working outdoors, and be attentive to signs of fatigue or strain.
Maintenance Tips for Extended Durability
A pavement breaker, like any tool, is an investment. Ensuring its durability not only saves costs in the long run but also ensures safety and efficiency during operations.
Regular Cleaning: Getting Rid of Dirt and Debris
The nature of the work that pavement breakers are involved in means they are constantly exposed to dirt, dust, concrete particles, and other debris. If left unchecked, these can accumulate and affect the tool’s performance.
Cleaning Methods:
- Post-Use Cleaning: After each use, give the breaker a basic clean. Use a brush to remove larger debris and a cloth to wipe down surfaces. Ensure the tool is switched off and unplugged (if electric) during this process.
- Deep Cleaning: Periodically, perhaps once a month or after a particularly intensive job, perform a more thorough cleaning. This can involve using compressed air to blow out fine particles from crevices, especially around the motor or moving parts.
- Check the Air Filters: For pneumatic breakers, the air filter can become clogged over time. Ensure it’s clean and replace if necessary.
- Lubrication Points: After cleaning, it’s a good time to check lubrication points and ensure they’re well-oiled to prevent friction and wear.
- Protective Finish: Consider using a silicone-based spray or protective finish to guard against moisture, especially if the tool will be stored for an extended period.
- Storage: After cleaning, store the pavement breaker in a dry, cool place. If it comes with a case or protective cover, use it. This prevents unnecessary exposure to elements and further accumulation of dust.
Wrapping Up
Pavement breakers are important tools instrumental in shaping and reshaping our urban landscapes. From the foundational understanding of their components and types to their safe operations and maintenance, a comprehensive knowledge of these powerful machines ensures efficiency, safety, and longevity in their applications.
But, as with all tools, the expertise lies not just in the equipment but also in the hands of the demolition contractors who use them. At Liberty Demolition, we don’t just demolish; we ensure efficient Waste Management and Recycling, which pave the way for an eco-friendly, sustainable future.
If you’re looking for professional demolition contractors in Philadelphia who understand the intricacies of demolition and uphold the highest standards in every project, look no further. Choose Liberty Demolition. Call us to learn more about our services.