A hydraulic concrete crusher is a tool designed for controlled demolition of concrete structures. It uses hydraulic pressure to break concrete and make removal or recycling easier.
Curious about how it works and where it’s used? Let’s get into the details.
What Is a Hydraulic Concrete Crusher?
A hydraulic concrete crusher, often used in the construction and demolition industries, is a heavy-duty tool that helps in the efficient and safe breakdown of concrete structures. These crushers are especially beneficial for projects that require the removal of large amounts of concrete.
The Anatomy of a Hydraulic Concrete Crusher
Understanding the anatomy of a hydraulic concrete crusher can provide a clearer insight into how this powerful tool operates and achieves its concrete-crushing objectives.
Hydraulic System and How It Generates Force
- Hydraulic Fluid Reservoir: At the base of every hydraulic system is a reservoir that holds the hydraulic fluid. This fluid is the lifeblood of the system and is responsible for transmitting force throughout the crusher.
- Pump: The hydraulic pump is responsible for moving the fluid from the reservoir and pushing it under pressure through the system. Depending on the design, pumps can either be manual or powered by electricity or internal combustion engines.
- Valves: These are used to control the direction, flow rate, and pressure of the hydraulic fluid. They can direct the fluid to different parts of the crusher, ensuring that force is applied precisely where it’s needed.
- Cylinders: As hydraulic fluid is pumped into a cylinder under pressure, a piston inside the cylinder moves. This movement is what generates the force to crush concrete. The more pressure applied, the greater the force exerted by the cylinder.
- Pipes and Hoses: These components transport the hydraulic fluid between the various parts of the system.
The working principle of the hydraulic system is based on Pascal’s Law, which states that any change in pressure applied at any point in a confined fluid is transmitted undiminished throughout the fluid. In the context of the crusher, when force is applied to the hydraulic fluid (by the pump), this force is transferred undiminished to the hydraulic cylinders. As the cylinders actuate, they exert a powerful crushing force on the concrete.
Crusher Jaws and Their Design Specifics
The jaws are typically made of high-strength, wear-resistant materials, often hardened steel or a composite of metals. This ensures they can withstand the immense pressure exerted during the crushing process and remain durable against abrasive concrete surfaces.
Depending on the specific application and the nature of the concrete to be crushed, the jaws can vary in design:
- Flat Jaws: These are used primarily for crushing flat, even surfaces. They provide a consistent crushing force and are often used in controlled demolition where precision is essential.
- Pointed or Sharp Jaws: Ideal for piercing through reinforced concrete or breaking apart tougher structures.
- Combination Jaws: These combine features of both flat and pointed jaws and offer versatility for varied demolition tasks.
The size of the jaws determines the volume of concrete the crusher can handle at once. Larger jaws can crush bigger chunks of concrete but might be more cumbersome and less precise, whereas smaller jaws offer precision but might require more cycles to crush a large structure.
The gap between the jaws determines the size of the crushed concrete pieces. Some crushers offer adjustable settings, allowing operators to change the gap based on the desired output size or crushing efficiency.
Given that reinforced concrete is common in many modern structures, crusher jaws often come with designs that can handle the steel rebar within the concrete. This might include stronger materials, sharper edges, or mechanisms that can cut or bend the rebar as the concrete is crushed.
Some crusher jaws are designed to move or articulate and provide better angles for crushing and ensuring that force is evenly distributed. This articulation can be crucial when working in confined spaces or when precise crushing is required.
Control and Safety Features
- Pressure Relief Valves: These valves automatically release any excess pressure to prevent the hydraulic system from over-pressurizing, which can lead to equipment failure or even injury.
- Emergency Stop Mechanism: Almost all hydraulic concrete crushers come with an emergency stop button or mechanism. In case of unforeseen circumstances or potential hazards, the operator can immediately halt the crusher’s operation to avoid accidents.
- Anti-Jamming Systems: These can detect obstructions and either reverse the crusher’s motion or halt operations to allow the obstruction to be safely removed.
- Guarding and Shields: These barriers protect the operator and bystanders from any flying debris or accidental contact with the machine while in operation.
- Audible and Visual Alarms: These alarms alert operators and those nearby of the crusher’s operations, especially when it starts or stops. They can also indicate system malfunctions to ensure timely interventions.
- Stability Features: Many crushers come with outriggers or stabilizing arms that can be deployed to ensure the equipment remains steady during operation.
- Hydraulic Fluid Monitoring: Low or contaminated fluid can impair the crusher’s function and can be a potential safety hazard. Regular monitoring ensures the system is always in optimal condition.
- Regular Inspection Indicators: Some modern crushers come with indicators that remind operators of regular maintenance checks.
- Operator Training: While not a physical feature of the crusher itself, knowledgeable operators are less likely to make errors, understand the machine’s limitations, and are better prepared to handle emergencies.
- Backup Systems: In the event of primary control system failures, backup or redundant systems can take over and ensure the crusher can still be safely operated or shut down.
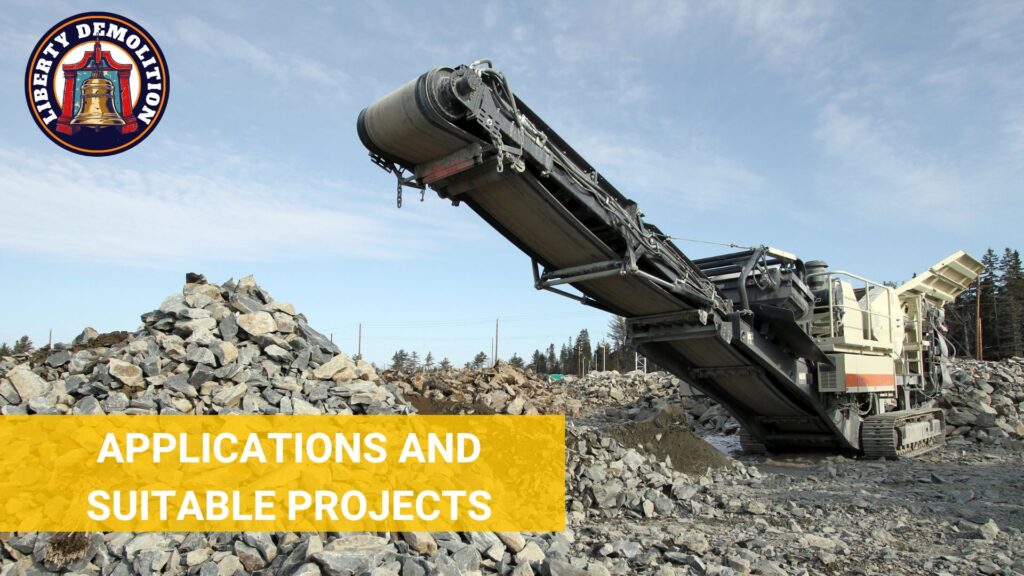
Applications and Suitable Projects
Here are some of the primary applications and suitable projects where these crushers are often used:
Breaking Down Large Concrete Structures Like Walls and Pillars
- Safety and Precision: Hydraulic concrete crushers offer a controlled method of breaking down these structures, which reduces the risk of unintended collapses that can occur with more aggressive demolition methods.
- Reinforced Concrete: In modern construction, walls and pillars often contain reinforcement bars (rebar) for added strength. Hydraulic concrete crushers are particularly good at handling this type of construction.
- Reducing Vibration and Noise: Hydraulic concrete crushers offer a quieter, less vibratory alternative to jackhammers or wrecking balls. This makes them ideal for operations in populated or delicate settings.
- Accessibility: The relatively compact design of many hydraulic concrete crushers allows them to be used in confined or hard-to-reach areas.
- Material Separation: The precision of hydraulic crushers can result in cleaner separation of concrete and rebar, which makes the subsequent processing or recycling steps more efficient.
- Environmentally Friendly: Hydraulic concrete crushers typically produce less airborne dust compared to other methods, which results in a cleaner job site.
- Cost-Effective: By reducing the need for additional machinery, minimizing damage to surrounding structures, and speeding up the demolition process, overall project costs can be optimized.
Tasks Where Precision is Crucial, Like Historical Sites
- Minimized Collateral Damage: In densely populated areas, the proximity of structures means that the margin for error is minimal. Hydraulic concrete crushers offer a more precise way of breaking down structures and ensure that only the targeted area is affected.
- Noise Reduction: Hydraulic concrete crushers operate more quietly than jackhammers or bulldozers.
- Dust Control: The controlled nature of the crusher’s operation results in less airborne dust, which is especially important in populated areas to maintain air quality and reduce health risks for residents.
- Preserving Historical Integrity: When working on or near historical sites, it’s crucial to preserve their integrity. The precision of hydraulic concrete crushers makes them ideal for such delicate tasks.
- Limiting Vibrations: In historical sites, vibrations from heavy machinery can jeopardize the structural integrity of old and potentially fragile structures. With its controlled and direct force, the hydraulic concrete crusher ensures that vibrations are localized and significantly reduced.
- Selective Demolition: Hydraulic concrete crushers can be used to selectively crush parts of a building, ensuring that only the desired sections are demolished.
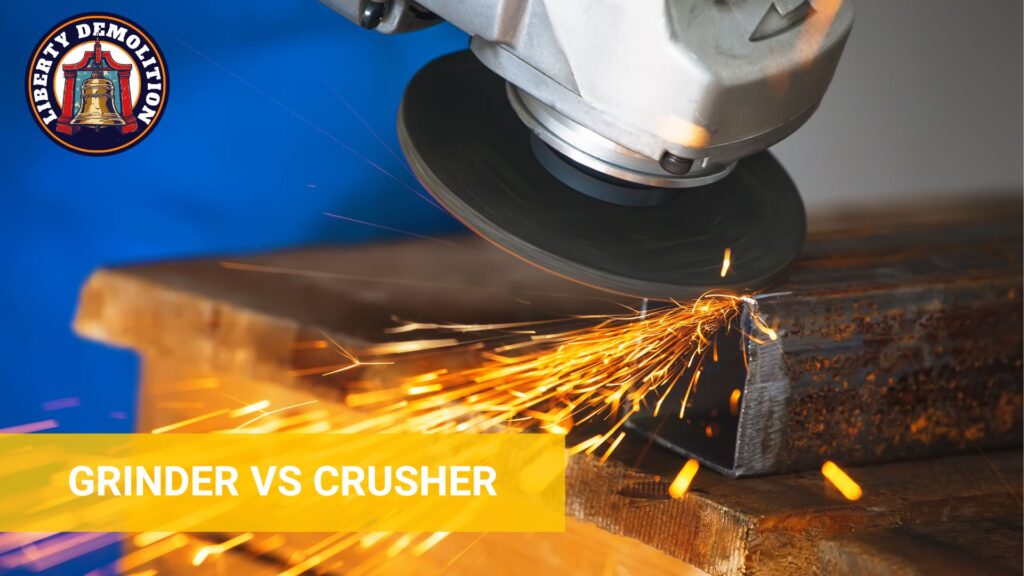
What is the Difference Between Grinder and Crusher?
While grinders and crushers share some similarities in their purpose (both are used to break down materials), they differ significantly in terms of their operation, design, and specific applications:
Feature | Crusher | Grinder |
Purpose and Mechanism | Breaks down large chunks of material. Uses force to squeeze, impact, or compress. | Grinds materials finely. Uses sharp blades or abrasive surfaces. |
Applications | Used in construction for breaking down rocks, concrete, etc. | Found in food processing for grains/spices, and industries needing fine particles. |
Output Consistency | Produces variable, larger, irregular chunks. | Produces consistent and fine output, uniform particle size. |
Design and Operation | Can be large machines (e.g., jaw crushers) or smaller devices. | Ranges from large industrial mills to small kitchen appliances. |
Force and Wear | Relies on compressive or impact forces; significant wear. | Employs shear or abrasive forces; different wear patterns. |
Versatility | Designed for specific materials; focused on breaking down. | Adjustable for different particle sizes; versatile applications. |
Safety and Precautions | Concerns about material ejection; needs strong safety barriers. | Risks from flying particles and heat; needs protective screens/cooling. |
Tips for Ensuring Safety During Operation
Safety is crucial when operating heavy machinery, especially tools as powerful as crushers. Implementing safe practices not only protects the operator but also ensures the longevity of the equipment and the well-being of everyone on the job site.
1. Proper Training
Before allowing anyone to operate a crusher, ensure they have undergone thorough training. This training should cover the equipment’s operation, safety protocols, emergency procedures, and basic maintenance checks.
2. Wear Protective Gear
Operators should always wear appropriate protective gear, including hard hats, safety glasses, ear protection, and steel-toed boots. This gear can help protect them from flying debris, loud noises, and other potential hazards.
3. Regular Inspections
Before starting the crusher, always conduct a thorough inspection. Check for any signs of wear, damage, or malfunction. Ensure all safety guards and shields are securely in place.
4. Stay Clear of Moving Parts
Never attempt to adjust or touch the machine’s moving parts while it’s in operation. If there’s a need to make adjustments or remove obstructions, always turn off the machine and wait for all components to come to a complete stop.
5. Use the Emergency Stop
Familiarize yourself and all operators with the crusher’s emergency stop mechanism. Don’t hesitate to use this feature in any situation that seems potentially hazardous.
6. Maintain a Clear Work Area
Ensure that the area around the crusher is free from unnecessary equipment, tools, or debris. A tidy workspace reduces the risk of tripping or other accidents.
7. Avoid Overloading
Always adhere to the crusher’s specified capacity limits. Overloading can lead to malfunctions, increased wear, or even dangerous equipment failures.
8. Dust Control
Crushing can produce significant dust. Use built-in dust suppression systems, or consider adding external methods, like water sprays, to keep dust levels down and protect operators from inhalation risks.
9. Secure the Crusher
Especially for mobile crushers, ensure that the machine is stabilized before operation. Some crushers come with stabilizing outriggers or similar features. Using them can prevent unwanted movement or tipping during operation.
10. Stay Updated
Manufacturers often release safety bulletins, updates, or recalls. Ensure you’re on their mailing list or regularly check their websites to stay updated on any new safety recommendations or required modifications.
11. Limit Unauthorized Access
Ensure that only trained personnel can access the crusher’s operation area. This can be achieved through fencing, barriers, or clear signage warning of the dangers.
12. Regular Maintenance
Keeping the crusher well-maintained ensures its efficiency and safety. Regularly replace worn-out parts, lubricate moving components, and address any signs of wear or damage immediately.
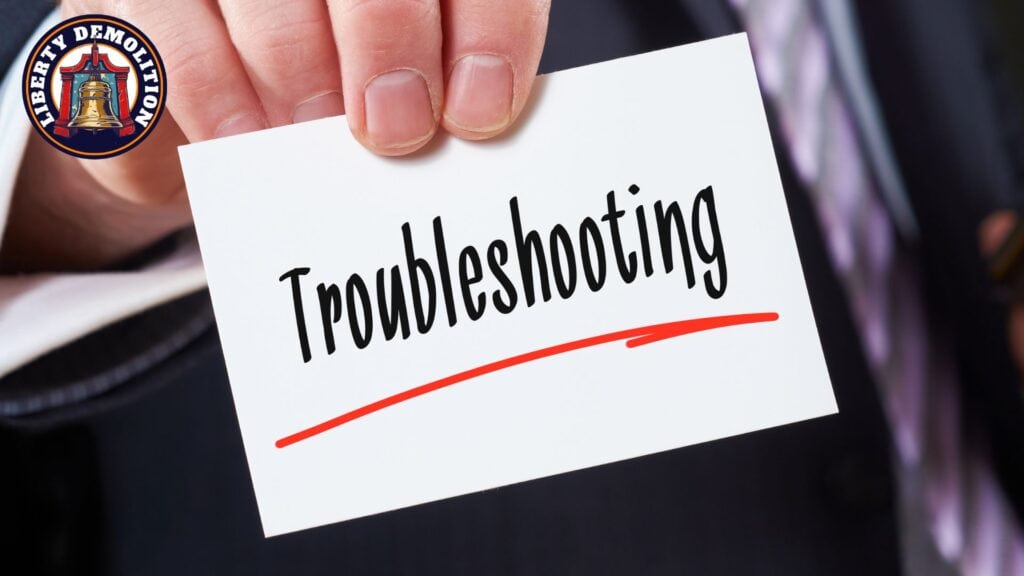
Maintenance and Troubleshooting
Regular maintenance and troubleshooting are critical for the longevity, efficiency, and safe operation of crushers. They can prevent costly breakdowns, extend the machine’s lifespan, and ensure optimal performance:
Routine Inspection and Cleaning
- Scheduled Inspections: This could be daily, weekly, or monthly, depending on the crusher’s usage frequency.
- Exterior Checks: Begin by examining the crusher’s exterior for any signs of damage. Pay particular attention to weld points and structural supports, which might bear the brunt of operational stresses.
- Operational Components: Inspect moving parts like jaws, hinges, and hydraulic systems. Look for signs of wear, misalignment, or unusual noises.
- Lubrication Levels: Regularly check the lubrication levels and the quality of the lubricants used.
- Hydraulic System: If the crusher is hydraulically operated, inspect the hydraulic lines for any signs of leaks or wear. Also, check the hydraulic fluid levels and replace or top up as necessary.
- Air Filters and Vents: Many crushers come equipped with air filtration systems to keep dust and debris from entering critical components. Ensure these filters are clean, and replace them if they show signs of excessive clogging.
- Electrical Systems: For crushers with electrical components, inspect wires, connectors, and control panels for any signs of damage, wear, or corrosion.
- Cleaning: After inspection, clean the crusher thoroughly. Remove any accumulated dust, debris, or foreign materials.
- Documentation: Maintain a log of all inspections and any maintenance activities undertaken.
- Safety: Before conducting any inspection or cleaning, ensure the crusher is turned off, disconnected from any power source, and fully immobilized.
Addressing Common Issues
Hydraulic Fluid Leaks:
Look for puddles of fluid under the machine, wet spots on hoses, or drops around connectors. If a leak is detected, shut down the machine immediately to prevent further leakage and potential pressure loss.
Replace damaged hoses or tighten loose connectors. If the issue persists, it might be due to worn seals or gaskets, which should be replaced. Always use manufacturer-recommended hydraulic fluid for top-ups or replacements.
Jaw Misalignment:
Uneven wear patterns, reduced crushing efficiency, or unusual noises during operation can indicate jaw misalignment. Stop the machine and conduct a visual inspection to confirm the misalignment.
Some crushers offer manual adjustment options for realignment. In others, components might need replacement or professional recalibration. Regularly check for signs of wear in mounting brackets or the jaw structure itself, as these can lead to misalignment.
Worn or Damaged Components:
Reduced efficiency, increased vibration, or unusual noises might point to worn components. Inspect the crusher for visibly worn or damaged parts. Replace any components showing significant wear. This might include jaws, bearings, hydraulic cylinders, or electrical components. Always source replacement parts from trusted suppliers to ensure compatibility and durability.
Electrical Issues:
These include intermittent machine operation, unexpected shutdowns, or non-responsive controls. Turn off the machine and disconnect it from the power source. Inspect wiring, connectors, and control panels for damage or wear. Reset circuit breakers or replace fuses if necessary. If electrical issues persist, consult with a qualified electrician or the manufacturer.
Overheating:
Shut down the machine to prevent damage. Check for blockages in ventilation or cooling systems. Ensure lubrication levels are adequate, as low lubricant can cause friction and overheating. If the crusher is hydraulic, inspect the hydraulic fluid.
Vibration Issues:
Turn off the machine to prevent further wear or damage. Inspect the crusher for loose components, imbalance in rotating parts, or material build-up that might be causing the vibration.
Long-Term Care for Extending Equipment Life
Scheduled Maintenance:
Just as regular health check-ups are vital for humans, scheduled maintenance ensures crushers remain in peak condition, addressing wear and tear before it escalates. Follow the manufacturer’s guidelines on maintenance schedules. This often includes tasks like lubrication, filter replacements, and bolt tightening.
Use Quality Parts and Fluids:
Using subpar or non-recommended parts and fluids can decrease equipment life and hamper performance. Always use manufacturer-recommended or equivalent-quality parts for replacements. For hydraulic crushers, ensure the hydraulic fluid is of the specified type and grade.
Store Properly:
Proper storage can protect the crusher from environmental factors that can accelerate wear, such as moisture, extreme temperatures, or contaminants. When not in use, store the crusher in a covered area, shielded from the elements. If this isn’t possible, consider using tarps or covers.
Regular Cleaning:
Dirt, debris, and accumulated materials can cause premature wear and reduce operational efficiency. Regularly clean the machine and make sure that material build-ups are cleared and all components are free from excessive dust and grime.
Protect Against Overloading:
Overloading can cause undue stress on the crusher’s components, which leads to faster wear and potential failures. Always adhere to the crusher’s capacity limits. Educate operators on the signs of overloading and the importance of avoiding it.
Update and Upgrade:
Technology and designs evolve. Staying updated can help in maintaining efficiency and equipment life. Keep an eye on manufacturer updates, software upgrades, or newer models. Sometimes, modifying older equipment with new components can extend its lifespan.
Keep Detailed Records:
A detailed maintenance and repair log helps predict potential issues, schedule preventive maintenance, and understand wear patterns. Document every inspection, maintenance activity, repair, and part replacement. This record will prove invaluable for troubleshooting and deciding when it might be more cost-effective to replace the machine.
Routine Operator Training:
Operator errors can lead to premature wear or damage. Regular training ensures operators are familiar with best practices and recent updates. Schedule refresher training sessions, especially after equipment upgrades or if new operational guidelines are introduced.
Wrapping Up
When employed correctly, hydraulic concrete crushers offer precision, safety, and environmental benefits that are unparalleled by many other demolition tools. However, like any equipment, their efficacy is tied to proper usage, maintenance, and care.
If you’re looking for professional demolition contractors in Philadelphia who embody excellence in every demolition project, look no further than Liberty Demolition. With a solid commitment to safety, environmental responsibility, and customer satisfaction, we implement an eco-friendly solution in every project that aligns with modern-day demands.
Don’t leave your next project to chance. Trust in the expertise and dedication that Liberty Demolition brings to the table. Reach out to us today.