A hydraulic hammer, often known as a breaker, is a powerful construction tool that uses pressurized fluid to produce controlled and concentrated force, designed primarily to break concrete, rocks, and other hard materials.
Curious to know more? Let’s get straight to it!
What Is a Hydraulic Hammer?
Simply put, a hydraulic hammer is a mechanical tool that utilizes the power of hydraulic pressure to generate impact energy. Think of it as a large, powerful hammer that’s operated by machinery, rather than manually.
What is a Hydraulic Hammer Used For?
The main function of a hydraulic hammer is to break down large rocks, concrete, and other hard materials often encountered on construction sites. This tool is especially valuable when the task at hand involves demolishing structures or paving the way for new construction. Whether it’s tearing down an old building or breaking up a roadway, the hydraulic hammer is the go-to equipment.
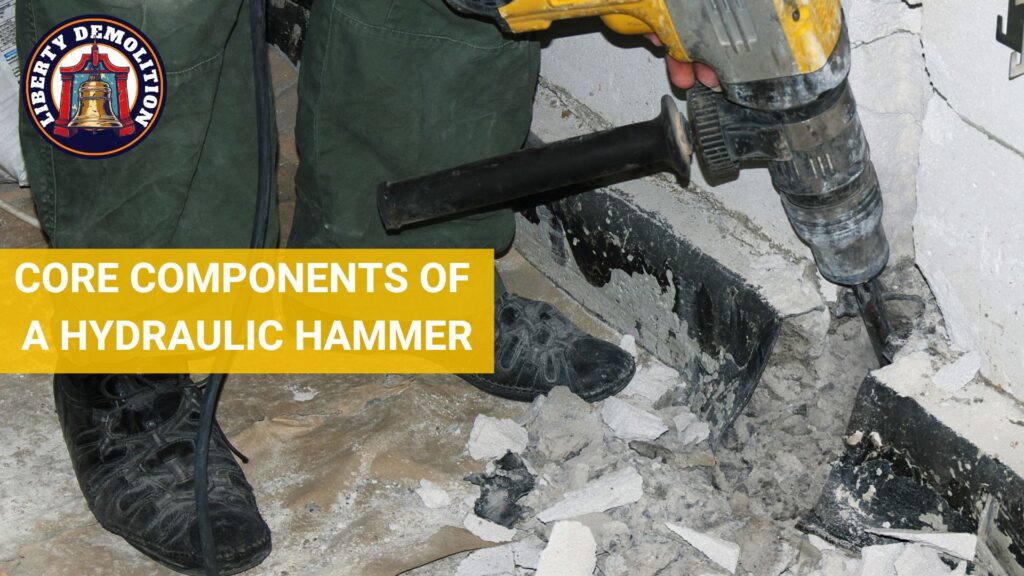
Core Components of a Hydraulic Hammer
A hydraulic hammer is more than just a massive tool that breaks things. It’s a meticulously designed piece of machinery with various components working together.
The Power Cell: Working Principle and Hydraulic Fluid
The Power Cell
This is where all the magic happens, so to speak. The power cell is the main component that generates and directs the hammer’s force to allow it to deliver those powerful blows to rocks and concrete.
Working Principle
The working principle of the power cell is fairly straightforward. When the hydraulic hammer is activated, hydraulic fluid (usually oil) is pushed under high pressure into the power cell. Inside, a piston is moved by this pressurized fluid. As the piston moves rapidly back and forth, it strikes a chisel or breaker tool attached to the hammer. This action, repeated many times a minute, creates the powerful impacts that the hydraulic hammer is known for.
Hydraulic Fluid
Hydraulic fluid plays an indispensable role in the functioning of a hydraulic hammer. It acts as both a lubricant and a medium to transfer force within the hammer.
Characteristics of Hydraulic Fluid:
- Incompressibility: When pressure is applied to it, unlike gasses, it doesn’t compress but instead transfers the force effectively. This ensures that the force exerted on one end (from the hydraulic system) is efficiently transferred to the other end (the hammer’s chisel).
- Lubrication: Apart from transmitting power, the hydraulic fluid also provides lubrication to the moving parts inside the hammer. This reduces wear and tear.
- Coolant: Hydraulic fluid acts as a coolant, absorbing the heat generated during the hammer’s operation. By doing so, it prevents the tool from overheating, which could damage the internal components.
Chisel or Bit: Types and Specific Uses
The chisel or bit is the part of the hydraulic hammer that comes into direct contact with the material being broken. It’s like the sharp edge of a manual hammer, taking all the energy from the power cell and focusing it on a specific point to do its job effectively. Over time, different types of chisels or bits have been developed, each designed for a specific purpose.
Moil Point Bit
The moil point bit has a tapered point, which makes it appear somewhat like a large, elongated pyramid. It’s the jack-of-all-trades and is suitable for a wide variety of applications, such as breaking concrete, tarmac, and even some types of softer rocks. Because of its versatility, it’s often the default choice for general construction and demolition tasks.
Flat Chisel Bit
This bit has a flat end. It’s broad and doesn’t taper to a point. The flat chisel is best for applications that require a more precise edge or where material needs to be sheared off in layers. It’s great for trimming excess concrete or for creating a smooth surface on a break.
Blunt Tool Bit
This bit is characterized by its rounded end, similar in shape to the end of a cylinder. The blunt tool bit is ideal for breaking large boulders or dense materials where a focused point isn’t necessary. Its design ensures energy is spread out over a larger surface area, which makes it effective for breaking massive rocks in quarries or mining operations.
Cross-Cutting Chisel
This chisel features a cross or X-shaped end, designed to give a multi-directional impact. It’s particularly handy for scoring or creating lines in rock or concrete. The cross-cutting chisel is often used for tasks that require predefined break lines, such as segmenting large blocks of stone.
In-line Chisel
This chisel is elongated with multiple ridges or grooves running parallel along its length. It’s designed for splitting materials in a straight line. The in-line chisel is a favorite for tasks like splitting logs or wooden beams.
Housing, Accumulator, and Control Valves
While the power cell and the chisel or bit play significant roles, other components of a hydraulic hammer are equally important for its overall functionality and efficiency.
Housing
The housing is the outer shell or casing that encloses the hammer’s internal components. Think of it as the protective barrier, safeguarding the vital parts inside. It primarily protects the inner components from external damage, be it from environmental factors like dirt and moisture, or from physical damage during operation.
It ensures that the internal components stay aligned and move in the desired manner. This alignment is crucial for the piston to strike the chisel effectively. The housing also acts as a noise dampener, as it reduces the noise levels generated during the hammer’s operation.
Accumulator
The accumulator is like a reserve tank for hydraulic fluid. It’s a crucial component that ensures the hammer operates smoothly and consistently. It stores hydraulic energy for future use. When there’s a sudden demand for more power than the hydraulic system can immediately provide, the accumulator releases its stored energy to compensate.
It acts as a cushion, absorbing hydraulic shocks. This not only protects the hydraulic system from potential damage but also ensures the hammer operates more smoothly. By releasing or storing hydraulic fluid, the accumulator helps maintain a consistent pressure in the system.
Control Valves
Control valves are components that regulate the flow of hydraulic fluid within the hammer. They’re like the traffic directors of the hydraulic world. The primary role of control valves is to regulate the flow of hydraulic fluid and direct it where it’s needed within the system.
They play a vital role in managing the pressure of the hydraulic fluid, to ensure it’s neither too high (which could damage components) nor too low (which could reduce efficiency). In case of excessive pressure, certain control valves act as relief valves, and redirect the fluid or release some of it to prevent potential damage to the system.
How Do Hydraulic Tools Work?
Hydraulic tools have revolutionized industries, from construction to automobile mechanics. But what drives these powerful tools?
What is the Principle of Hydraulic Lift?
Hydraulic lift systems leverage a simple but effective principle: Pascal’s Law. This law states that any change in the pressure applied at any point in a confined incompressible fluid is transmitted undiminished throughout the fluid in all directions.
Key Aspects:
- Confined Fluid: For a hydraulic system to work, the fluid must be confined, which means it’s trapped inside a system of pistons and cylinders.
- Pressure Application: When pressure is applied to the fluid at one point (usually by pressing a piston), this pressure is transmitted undiminished throughout the entire system.
- Force Amplification: Given that the force exerted by the fluid is the product of its pressure and the area of the piston it acts upon, a small piston can be used to exert a small force (and therefore a small pressure) on one end. This pressure can be used to lift a much larger weight on the other end if a larger piston is used.
What is the Principle of Hydraulic Control?
Hydraulic control systems are all about precision and direction. The principle here revolves around the controlled flow and pressure of hydraulic fluids to achieve desired outcomes.
Key Aspects:
- Valves: These are integral components that determine the direction, flow rate, and pressure of the hydraulic fluid. Depending on their settings, they can either allow fluid to flow, stop it, or direct it to different parts of a system.
- Feedback Mechanisms: Many advanced hydraulic control systems incorporate feedback mechanisms. These can measure various factors like pressure, temperature, or flow rate and adjust the system’s operation in real-time for optimal performance.
- Force and Movement Control: Hydraulic control systems can be designed to maintain constant force (like in presses) or constant speed (like in certain types of motors). This is achieved by constantly monitoring the output and adjusting the flow and pressure of the hydraulic fluid accordingly.
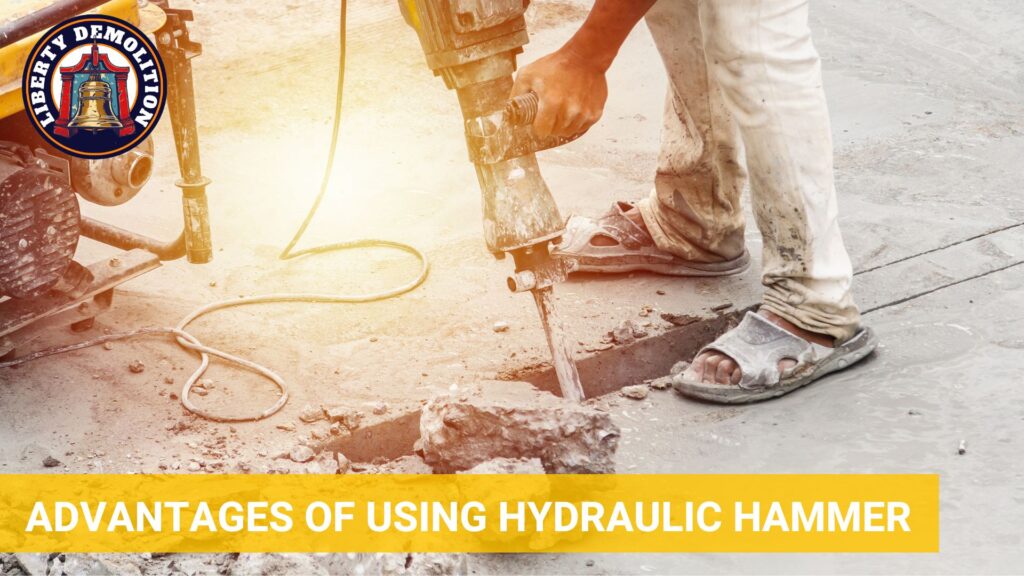
Advantages of Using Hydraulic Hammers
In the construction and demolition industries, tools are designed to accomplish tasks with maximum efficiency and minimum hassle. Among these tools, hydraulic hammers stand out for the following reasons:
High Efficiency in Breaking Tough Surfaces
- Power-Packed Performance: Their design, leveraging the might of hydraulic force, ensures they can exert tremendous pressure on a specific point. This makes them incredibly effective at breaking tough surfaces like concrete, rocks, and asphalt.
- Continuous Operation: Unlike manual tools which rely on repeated human effort, hydraulic hammers offer continuous operation.
- Less Fatigue: Given that the machine does most of the heavy lifting, there’s significantly less fatigue on the operator’s part.
Adaptability: Compatibility with Various Carriers
- Wide Range of Carriers: These hammers can be easily attached to a variety of carriers, including excavators, backhoes, skid steers, and more. This makes them incredibly versatile, as they can be used on whatever machinery is available or most suitable for a particular job.
- Different Sizes for Different Jobs: Hydraulic hammers come in various sizes, from smaller models suitable for light tasks and compact carriers, to massive units designed for large excavators and major demolition jobs.
Precision and Reduced Noise Compared to Other Tools
- Accurate Demolition: Unlike some other demolition tools that might cause collateral damage, hydraulic hammers are precise. Their focused impact means they break what they’re supposed to without causing unnecessary destruction to surrounding structures or materials.
- Noise Reduction: While no heavy machinery is entirely silent, hydraulic hammers are designed to produce less noise compared to many other demolition tools.
- Less Vibrations: The efficient design of hydraulic hammers means they produce fewer vibrations compared to some other tools.
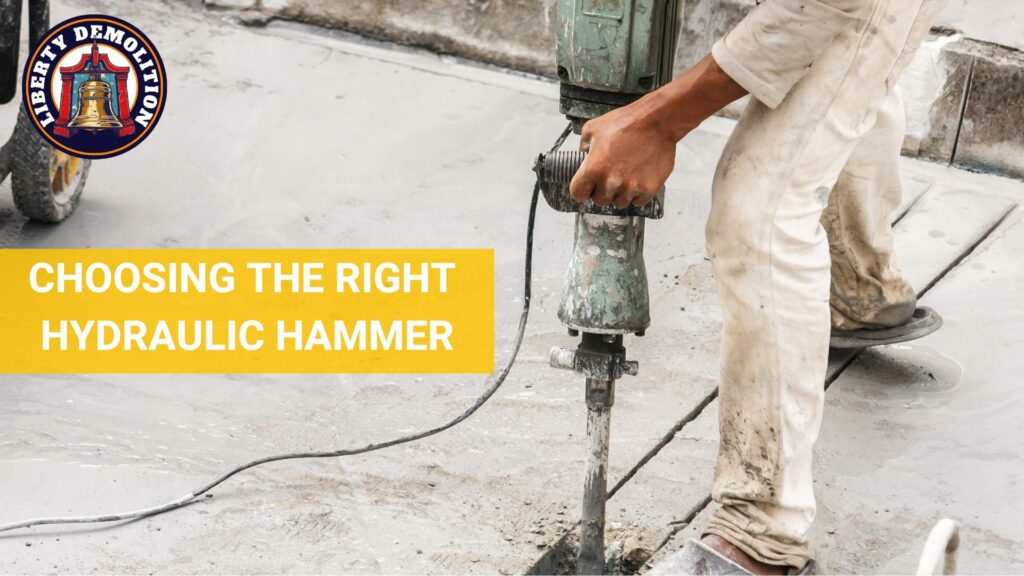
Selecting the Right Hydraulic Hammer for Your Project
Here’s what to consider when selecting the perfect hydraulic hammer for your task.
Sizing and Compatibility with Carriers
1. Determine the Carrier’s Specifications
Before selecting a hydraulic hammer, you need to fully understand the specifications of the carrier it will be mounted on. Some key specifications to consider include:
- Operating Weight: This is the total weight of the carrier when it’s equipped with all accessories and is filled with fluids. The hydraulic hammer’s size should be compatible with the operating weight of the carrier to ensure stability during operations.
- Hydraulic Flow and Pressure: Different carriers have different hydraulic flow rates (measured in gallons per minute) and pressure capabilities (measured in psi). It’s crucial to choose a hammer that matches these specs.
2. Understand the Work Environment
- Material Type: Are you breaking soft rock, hard rock, concrete, or asphalt? Different materials might require hammers of varying sizes and power.
- Volume of Work: If you have a large volume of material to break, you might lean towards a larger hammer to expedite the process, but for smaller tasks or in confined spaces, a smaller hammer might be more appropriate.
3. Evaluate Hammer Specifications
- Energy Class: This refers to the energy with which the hammer hits. It’s often measured in foot-pounds and is a good indicator of the hammer’s breaking power.
- Frequency: This indicates how often the hammer can strike in a given timeframe. A higher frequency can be beneficial for breaking softer materials, while harder materials might require a hammer with a higher energy class but a lower frequency.
4. Seek Expert Advice
If in doubt, it’s always beneficial to seek the advice of experts or professionals in the field. They can provide insights based on experience and can guide you towards making an informed decision.
5. Consider Future Projects
While it’s important to choose a hammer for your current needs, it’s also wise to consider potential future projects. If you anticipate taking on a variety of tasks in the future, you might lean towards a more versatile hydraulic hammer that can handle different materials and environments.
Energy Output and Frequency Considerations
When evaluating hydraulic hammers, two of the most critical factors to take into account are the tool’s energy output and frequency. These determine not only the power of the hammer but also its efficiency in various tasks.
1. Energy Output
Energy output, often referred to as the “energy class”, indicates the amount of energy the hammer delivers with each blow. It is typically measured in foot-pounds or joules. It determines the hammer’s breaking power. A higher energy output means the hammer can break tougher materials more effectively.
For projects involving dense materials like hard rock or thick concrete slabs, a hammer with a high energy output is necessary. Conversely, for softer materials or tasks that require a gentler touch, a lower energy output may be enough.
2. Frequency
Frequency refers to the number of blows a hydraulic hammer can deliver in a set period, typically measured in blows per minute (bpm). It can affect the speed at which a material is broken down. Hammers with a higher frequency can work through materials faster, but they might deliver less force per blow.
There’s often a trade-off between energy output and frequency. A hammer with a high energy output might have a lower frequency and vice versa. The key is to find a balance suitable for your specific task. For example, softer materials might be broken more efficiently with a high-frequency, lower-energy hammer, while harder materials require the opposite.
Auxiliary Features: Auto-lubrication, Noise Reduction, etc.
Modern hydraulic hammers come equipped with a range of auxiliary features that enhance their functionality, increase their lifespan, and improve user experience.
1. Auto-lubrication
Auto-lubrication systems automatically provide lubrication to the hammer, ensuring its components function smoothly. This feature reduces wear and tear, prolonging the hammer’s lifespan. It also reduces the need for frequent manual lubrication, saving time and ensuring consistent performance.
2. Noise Reduction
Some hydraulic hammers are designed with noise-dampening materials or structures that reduce the noise produced during operation. This is particularly beneficial in urban settings or areas where noise pollution might be a concern. It ensures compliance with noise regulations and reduces disturbances to nearby residents or other workers.
3. Anti-blank Firing
This feature prevents the hammer from firing when it’s not in contact with a material. Blank firing, or firing in the air, can cause significant damage to the hammer. It prolongs the lifespan of the hammer, reduces maintenance costs, and ensures safer operation.
4. Shock Absorption
Advanced hammers come with features that absorb the shock generated during operation, which reduces the impact on the carrier and the operator. This results in less wear and tear on the carrier, a more comfortable experience for the operator, and a more stable operation overall.
Leading Brands and Hydraulic Hammer Models
Here’s an overview of the top manufacturers and their standout models in the hydraulic hammer landscape:
1. Atlas Copco SB 702 Hydraulic Breaker
Atlas Copco is a globally recognized brand, known for its wide range of industrial tools. The SB 702 breaker is popular for its power and adaptability, suitable for a variety of tasks from demolition to excavation.
- Features: AutoStart, EnergyRecovery, air-venting valve, solid housing design.
- Pros: High reliability, versatile, suitable for a wide range of carriers, low maintenance.
- Cons: Might be overpowered for very light tasks.
2. Caterpillar H120E Hammer
Caterpillar, or Cat, is synonymous with heavy-duty machinery. Their H120Es hammer is known for its robust design and is effective in both quarrying and construction environments.
- Features: Automatic shut-off, energy chamber with diaphragm, sound suppression for reduced noise levels.
- Pros: High breaking power, reduced noise pollution, longevity.
- Cons: On the heavier side, may not be suitable for smaller carriers.
3. JCB HM25 LV
JCB is a household name in construction equipment. The HM25 LV is favored for its compact design and versatility, especially in urban and confined spaces.
- Features: Vibration dampened tie rods, hybrid technology, optimized power-to-weight ratio.
- Pros: Compact and lightweight, minimized operator fatigue, great for confined spaces.
- Cons: Might not be ideal for very heavy-duty tasks.
4. Bobcat HB980 Breaker
Bobcat, while famous for their skid steers, also offers a compelling lineup of hydraulic hammers. The HB980 breaker stands out for its high flow rate and efficient energy recovery system.
- Features: Nitrogen-charged backhead, unique valve design, energy recovery system.
- Pros: Quick cycle time, efficient energy usage, reduced recoil.
- Cons: Requires regular maintenance checks to ensure peak performance.
5. Komatsu WB97S
Komatsu is a giant in the construction machinery world. The WB07S is renowned for its durability and high energy output, suitable for breaking even the toughest materials.
- Features: Anti-blank firing system, vibration dampening, energy recovery mechanism.
- Pros: Extremely durable, high energy output, safety features.
- Cons: Might be overkill for smaller tasks or projects.
Wrapping Up
With their incredible force, precision, and adaptability, hydraulic hammers play a crucial role in efficiently breaking through tough materials, which paves the way for new constructions and developments. If you’re looking for expertise in the field of demolition, look no further than Liberty Demolition.
Our team of professional demolition contractors is dedicated to providing top-notch services that include residential, commercial, industrial, and selective demolition. We’re not just about tearing things down; we prioritize safety and environmental responsibility. We implement solid waste management and recycling processes and guarantee an eco-friendly solution tailored to your specific needs. Call Liberty Demolition today.