A rock breaker is a powerful tool or machine designed specifically to break large rocks into smaller, manageable pieces. Typically used in mining, construction, and quarrying, rock breakers play an important role in these industries.
Curious about the ins and outs of rock breakers? Let’s learn more about this powerful machine.
What is a Rock Breaker?
A rock breaker, as its name suggests, is all about breaking rocks. It’s a specialized piece of equipment tailored for the tough job of splitting big boulders and rocks into smaller fragments. Imagine trying to hammer down a gigantic rock with just a hand-held hammer; it would be impossible, right? That’s where you will need a rock breaker.
It’s not just the mining sector that relies on rock breakers. They’re widely used in construction, especially when laying the foundation for buildings, roads, or bridges. Quarrying is another industry where these powerful tools come in handy.
While explosives can do the job of breaking rocks, they come with their own set of challenges. Safety concerns, environmental issues, and precision are some factors where rock breakers have an edge. Not to mention, rock breakers allow for controlled demolition, ensuring the surrounding area remains undisturbed.
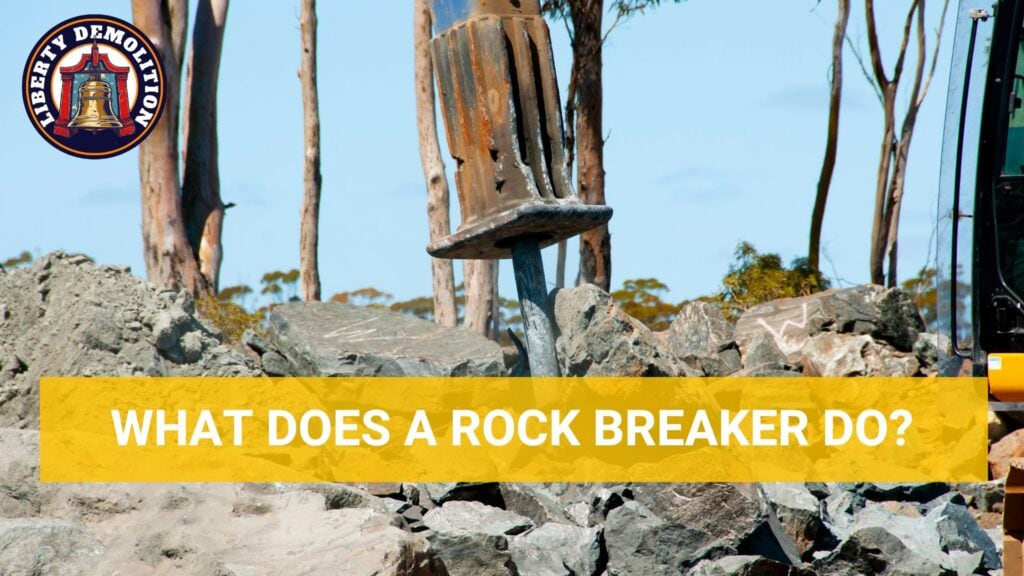
What Does a Rock Breaker Do?
A rock breaker fractures and breaks down large masses of rocks into more manageable sizes. But its applications and functions are much broader than this basic description:
- Fragmentation of Massive Rocks
In construction, mining, or quarrying, having rocks in smaller, workable sizes makes transportation and further processing significantly easier.
- Controlled Demolition
Unlike explosives, which can be unpredictable and cause collateral damage, rock breakers provide precision. It offers a controlled approach to demolition, ensuring only the targeted area is affected.
- Trenching and Excavation
When laying pipes, cables, or foundations, trenches are often required. Rock breakers can assist in creating these trenches, especially when the ground is hard or rocky.
- Secondary Rock Breaking
After primary blasting in mining or quarrying, there might still be oversized rocks that need further breaking. Instead of using another round of expensive and dangerous explosives, rock breakers are used to achieve the desired rock size for transportation or processing.
- Boulder Removal in Agriculture
Farmers occasionally encounter large boulders in their fields. A rock breaker can be used to break them down to make the land more cultivable.
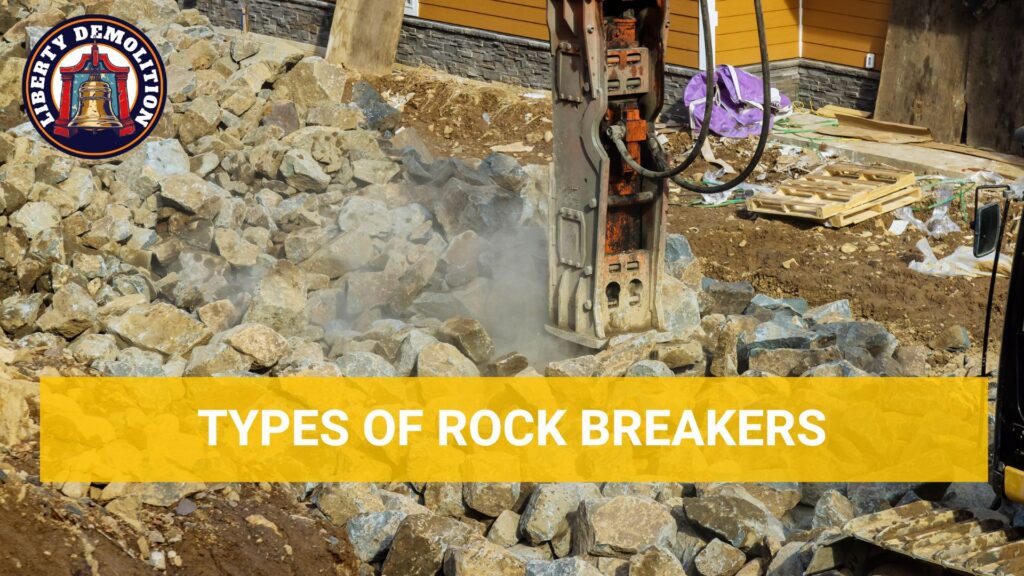
Types of Rock Breakers
Different designs of rock breakers have varying applications, each with its own set of advantages.
Top Type
The Top Type rock breaker is designed with the bracket positioned on the top of the tool. This design has several unique features:
- Compact Structure: With its compact design, you can use it in tighter spaces where other rock breakers might struggle.
- Versatility: The top type is well-suited for a wide range of applications, from construction to demolition and quarrying.
- Better Weight Distribution: The top-mounting ensures that the breaker’s weight is evenly distributed, which can minimize the wear and tear on the excavator arm or carrier.
- Ease of Maintenance: Its simpler structure means fewer components can go wrong.
Side Type
The Side Type rock breaker attaches to the side of the excavator or carrier. This type of rock breaker also has its distinct characteristics:
- Narrow Profile: The side-mounting provides a slimmer profile, particularly useful when working in narrow trenches or tight spaces.
- Reduced Noise: Typically, side type breakers are quieter than their counterparts.
- Less Vibrations: This type of rock breaker tends to produce fewer vibrations. This can be less taxing on the equipment and operator.
- Optimized for Specific Tasks: While versatile, side type rock breakers are often optimized for specific jobs like trenching or precise demolition.
Box Type
The Box Type rock breaker comes with a housing that surrounds the breaker, giving it a box-like appearance. Here’s what sets the box type apart:
- Enhanced Noise Suppression: The primary advantage of the box type is its ability to dampen the noise. The enclosed structure acts as a sound barrier.
- Dust Suppression: The design also limits the spread of dust during operation, which results in a cleaner work environment and reduces environmental impact.
- Protection: The boxed enclosure increases its lifespan by shielding it from external elements and potential damage.
- Reduced Vibrations
Silent Type
The Silent Type rock breaker, often mistaken for the box type due to its quiet operation, is distinct in its own right. Here are its key features:
- Superior Noise Reduction: It is designed specifically to operate with minimal noise.
- Enhanced Efficiency: Many silent type rock breakers come with advanced hydraulic technology, which ensures efficient rock breaking with fewer strokes.
- Optimal for Urban Areas: Due to their quiet operation, silent type rock breakers are ideal for urban construction sites, road maintenance, or any project in noise-sensitive areas.
- Safety: With a focus on minimizing disruptions, silent type breakers often come with added safety features.
Backhoe Type
The Backhoe Type rock breaker is specifically designed for backhoe loaders. Here’s what you should know about this type:
- Versatility in Operation: Being fitted on backhoe loaders, which can handle digging, trenching, back-filling, and material handling, adding a rock breaker enhances its capability, making it a comprehensive earth-moving solution.
- Convenient Transition: One of the advantages of a backhoe type rock breaker is the ease of switching between the bucket and the breaker, which allows operators to dig and break without the need to use multiple machines.
- Cost-Efficient: For small to medium projects, investing in a backhoe loader with a rock breaker attachment can be more cost-effective than investing in a separate excavator and rock breaker.
- Perfect for Urban Jobs: Given the relatively smaller footprint of backhoe loaders, backhoe type rock breakers are suitable for urban jobs or smaller sites where space is a constraint.
Rammer Type
Rammer Type rock breakers are synonymous with high quality, high performance, and relentless reliability. Here’s what sets them apart:
- Power and Efficiency: Known for delivering high impact energy, rammers are designed for tough jobs.
- Durability: With wear-resistant parts and robust construction, they are engineered to withstand rugged terrains and prolonged use.
- Minimal Maintenance: Rammer type rock breakers are crafted to operate flawlessly with minimal downtime.
- Safety: With features like vibration dampening and noise reduction, rammers ensure operators can work safely.
Hydraulic Crusher
Hydraulic Crushers, while sometimes classified alongside rock breakers, focus more on crushing and pulverizing than just breaking. Here’s the rundown on hydraulic crushers:
- Efficient Crushing Mechanism: Hydraulic crushers are designed to crush and process various materials, including rocks, concrete, and steel.
- Variable Jaw Configurations: Different jaw types can be fitted based on the task at hand — cutting through rebar, crushing concrete, or pulverizing rocks.
- Self-regulating: The hydraulic nature ensures that the crushing force is automatically regulated. The crusher can adjust its pressure based on the resistance of the material.
- Safety and Precision: With their controlled operation, hydraulic crushers reduce the risk associated with unpredictable projectiles, which can be an issue with other breaking methods.
Vibratory Plate Compactor
Distinct from rock breakers, the Vibratory Plate Compactor is primarily used to compact soil, gravel, or asphalt. However, when attached to an excavator, they can be used for compacting rock in some settings. Here’s a closer look:
- Soil and Material Compaction: These compactors are perfect for creating solid and level grounds by generating consistent vibratory forces.
- Versatility in Application: Whether prepping for a road, laying the groundwork for a building, or setting up pavements, vibratory plate compactors ensure the underlying materials are compact and void-free.
- Time-efficient: Given their mechanized nature, these compactors can cover large areas quickly.
- Compact Design: Typically, vibratory plate compactors are smaller than other heavy machinery, which makes them suitable for projects with space constraints.
Pile Driver
Pile Drivers are specialized equipment used primarily for driving piles into the soil to provide foundational support for structures like buildings, bridges, and piers. Here’s what you need to know about pile drivers:
- Foundation Support: By driving piles deep into the ground, they transfer the structure’s load to the more solid layers of the earth.
- Types of Pile Drivers: There are various types of pile drivers, including drop hammers, diesel hammers, hydraulic hammers, and vibratory pile drivers. Each has its own mechanism and is suitable for different applications.
- Precision and Depth: Modern pile drivers come equipped with technology that ensures that piles are driven to the exact required depth with precision.
- Environmentally Friendly Options: Concerns about noise and vibrations have led to the development of more environmentally friendly pile driving methods, such as hydraulic pressing, which causes minimal disturbances.
- Multi-functional: Some modern pile drivers can also extract old piles.
Here’s a table summarizing the different types of rock breakers and their respective features and uses:
Types of Breaker | Best Features | When to Use |
Top Type | Compact structure, versatile, better weight distribution, easy maintenance. | Construction, demolition, and quarrying; when working in tighter spaces. |
Side Type | Narrow profile, reduced noise, less vibrations, optimized for specific tasks. | Narrow trenches, tight spaces, precise demolition, urban settings. |
Box Type | Enhanced noise suppression, dust suppression, protective enclosure, reduced vibrations. | Urban areas, noise-sensitive zones, challenging environmental conditions. |
Silent Type | Superior noise reduction, enhanced efficiency, optimal for urban areas, increased safety. | Urban construction, noise-sensitive environments, projects near residential zones. |
Backhoe Type | Versatility in operation, convenient transition, cost-efficient, perfect for urban jobs. | Urban job sites, small to medium projects, versatile construction needs. |
Rammer Type | Power & efficiency, durability, minimal maintenance, safety features. | Tough terrains, prolonged use, environments requiring consistent power. |
Hydraulic Crusher | Efficient crushing mechanism, variable jaw configurations, self-regulating, precision in demolition. | Demolition, recycling operations, specific crushing tasks. |
Vibratory Plate Compactor | Soil and material compaction, versatility in application, time-efficient, compact design. | Soil, gravel, or asphalt compaction; projects with space constraints. |
Pile Driver | Foundation support, precision & depth, various types available, environmentally friendly options, multi-functional. | Providing foundational support for structures in areas with weak or inconsistent soils. |
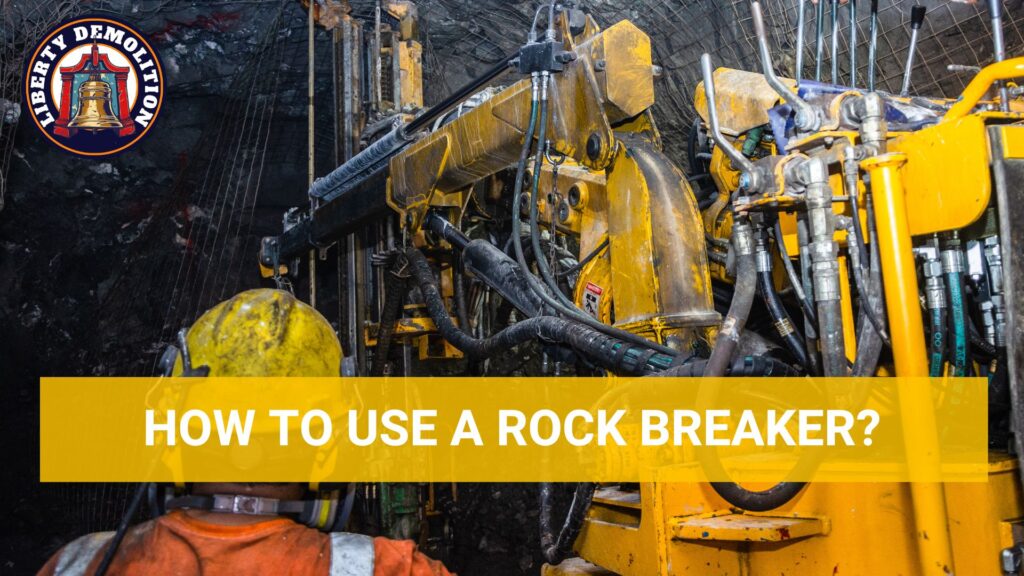
How to Use a Rock Breaker?
Using a rock breaker efficiently and safely requires understanding its operation and adhering to recommended procedures:
1. Safety First
Wear appropriate personal protective equipment (PPE), including a hard hat, safety glasses, ear protection, and steel-toed boots. Make sure that the work area is clear of unnecessary personnel and obstacles.
2. Equipment Inspection
Check the rock breaker for any visible damages or wear. Make sure all connections and fittings are tight, and check that the hydraulic fluid is at the recommended level.
3. Attach the Rock Breaker
If not already attached, connect the rock breaker to the excavator or the machine you’re using. Follow the manufacturer’s instructions for proper attachment.
4. Position the Machine
Move the machine into the position of a stable footing. Check that the breaker’s chisel point is perpendicular to the surface you intend to break.
5. Start Breaking
Begin with a series of short bursts to create a starting point. Once you have a starting hole, insert the breaker’s chisel into it for more effective breaking.
6. Work Methodically
Work in a systematic pattern and break the rock or concrete piece by piece. Avoid prying with the tool, as it may damage the breaker or the machine.
7. Periodic Checks
Periodically stop and inspect the breaker’s chisel for signs of wear or damage. Check the hydraulic system for any leaks or issues.
8. Complete the Job
Switch off the hydraulic breaker once you’ve broken up the desired amount. Clear away debris, ensuring safety in the work area.
9. Detach and Store
If you’re done for the day or moving to another task, carefully detach the rock breaker following the manufacturer’s instructions. Store the rock breaker in a safe location, away from moisture and potential damage.
Choosing the Right Rock Breaker for Your Needs
Here’s a guide to help you make an informed decision when choosing the most suitable rock breaker for your task at hand:
Evaluate Your Requirements
- Project Scale: A large mining operation has different needs than a smaller urban construction project. Understand the magnitude and duration of your project.
- Material Type: Are you breaking soft limestone, dense concrete, or hard granite? The toughness and composition of the material matter.
Carrier Machine Compatibility
- Machine Type: Whether using an excavator, backhoe loader, or skid steer, ensure the rock breaker is compatible.
- Carrier Weight: Rock breakers are designed for specific weight ranges. Matching the breaker to the carrier’s weight ensures optimal performance and safety.
Breaker Specifications
- Energy Impact: Measured in joules or foot-pounds, this indicates the breaker’s power. Harder materials require higher impact energy.
- Frequency: Some materials break more efficiently with rapid, light blows, while others need slower, powerful strikes.
- Tool Diameter: A larger tool diameter might be necessary for tougher jobs.
Operational Environment
- Noise Restrictions: In noise-sensitive areas, opt for silent-type or box-type breakers.
- Space Constraints: If working in a tight space, side-type or top-type breakers may be more suitable due to their profiles.
Ease of Maintenance
- Accessible Parts: Consider how easy it is to access parts for regular maintenance or replacements.
- Manufacturer Support: Choose brands with sufficient customer service and readily available parts.
Safety Features
- Anti-blank fire
- Vibration and Noise Dampening
Cost Considerations
- Initial Investment: While important, don’t let the initial cost be the sole factor in choosing. A cheaper breaker might cost more in maintenance in the long run.
- Operational Costs: Consider fuel consumption, maintenance frequency, and potential downtime.
Brand Reputation
- Choose brands known for durability, performance, and good customer support.
Safety Tips in Using Rock Breaker
Given the high forces and potential risks associated with rock breakers, it’s important to ensure that all safety measures are in place to protect the operator and the environment.
Wear Appropriate Personal Protective Equipment (PPE)
Personal Protective Equipment is a critical barrier between the operator and potential hazards during rock breaking operations. Here are the PPEs you must have:
- Hard hat
- Safety glasses or face shields
- Hearing protection (earplugs or earmuffs)
- Steel-toed boots
- High-visibility clothing
- Vibration-reducing gloves
Inspect the Equipment Before Use
Here are the key areas to Inspect:
- Hydraulic Systems: Examine hydraulic lines for any signs of leaks, damage, or wear.
- Tool/Chisel: Check for any signs of excessive wear, cracks, or deformities.
- Mounting Bracket: A loose or damaged bracket can lead to the breaker detaching unexpectedly.
- Bolts and Fasteners: Loose bolts can result in parts coming off during operation.
- Hoses and Connectors: Inspect for any leaks, cracks, or wear.
Follow the Manufacturer’s Instruction
Every rock breaker model is unique, with its specifications, operational limits, and maintenance requirements. Manufacturers design their equipment to function safely within specified operational limits. Going beyond these limits can endanger operators and those in the vicinity.
Proper use and maintenance, as per manufacturer instructions, can prolong the life of the rock breaker and save costs in the long run. Moreover, misuse or failure to adhere to manufacturer guidelines can void warranties.
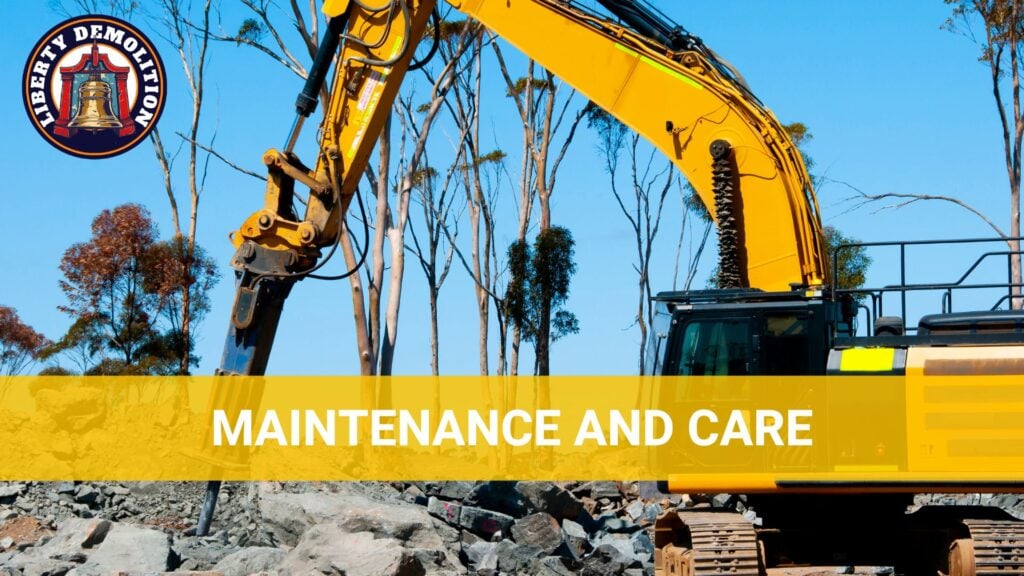
Maintenance and Care of Rock Breakers
Like any machinery, neglecting maintenance can lead to performance issues, safety risks, and potentially costly repairs.
- Regular Lubrication
Lubrication reduces friction between moving parts, minimizing wear and tear. Depending on the model, you might need to lubricate the breaker at the start of each job or specified intervals. Use the manufacturer-recommended grease. Moly-based greases are generally recommended due to their high-load carrying capabilities.
- Inspect the Tool/Chisel Regularly
The tool is subject to extensive wear. Look for cracks, wear, and blunt edges. Rotate or replace the chisel as needed.
- Check Hydraulic Fluids
Hydraulic fluid transfers power within the breaker. Regularly check fluid levels and ensure they are within manufacturer-recommended limits. Change fluids at intervals specified by the manufacturer.
- Inspect and Clean Hydraulic Filters
Check filters regularly and clean or replace them as per manufacturer guidelines. Clogged filters can increase internal temperatures and reduce efficiency.
- Monitor Nitrogen Pressure
Many rock breakers use a nitrogen gas assist system to boost power. Regularly check the nitrogen pressure and recharge if it falls below the recommended levels.
- Examine Hoses and Connectors
Worn-out hoses and connectors can leak and reduce power and efficiency. Regularly inspect for wear, cracks, or damage. Replace any compromised parts immediately.
- Proper Storage
It prevents unwanted moisture exposure, which can cause rust. After use, clean the breaker of any debris or dust. Store in a dry, sheltered place. If storing for extended periods, cover the breaker to protect it from dirt and moisture.
- Regular Professional Service
An expert can spot issues that might be missed during routine checks. Periodically, especially after intense jobs, have the breaker serviced by professionals.
Which Rock Breaker Is Best: Recommendations
While determining the right type of rock breaker is crucial, choosing a quality product from a reputed brand is equally important. Here are some top product recommendations based on industry reputation, performance, and user reviews:
For Large Scale Mining Operations: Atlas Copco HB 7000 DP
- Features: High performance, auto-lubrication, double percussion, and energy recovery system.
- Best For: Its robust design is perfect for heavy-duty mining applications.
For Urban Construction Projects: Soosan SB Series (Silent Type)
- Features: Reduced noise and vibration, enhanced durability, and suitable for various carriers.
- Best For: Urban projects where noise pollution is a concern.
Compact Spaces: Kubota KX018
- Features: Compact design, auto-lubrication, and high power-to-weight ratio.
- Best For: Tight spaces and high-performance requirements.
Versatile Needs: JCB HM380 (Backhoe Type)
- Features: Versatile design, energy-regenerative hydraulic system, and low maintenance.
- Best For: Varied tasks like excavation, trenching, and demolition.
Budget-Friendly Option: Bobcat HB1180 (Top Type)
- Features: Reliable performance, minimal maintenance, and suitable for medium-duty applications.
- Best For: Those seeking a balance between cost and performance.
For Road Construction and Soil Compaction: Wacker Neuson DPU 4545 (Vibratory Plate Compactor)
- Features: High compaction force, easy to maneuver, and user-friendly controls.
- Best For: Road constructions and soil compaction tasks.
Trust the Experts
A rock breaker is an indispensable tool for various industries, including mining, construction, and quarrying. It excels in breaking down massive rocks into manageable sizes and offers precise and controlled demolition while minimizing safety and environmental concerns.
If you think the task at hand that requires a rock breaker is too much for you, it is best to hand it down to the professional demolition contractors. We at Liberty Demolition are experts in demolition, clearing, and cleaning jobs. Aside from our comprehensive demolition services in Philadelphia (residential, commercial, industrial, and selective demolition), we excel in efficient waste management and recycling.
So, what are you waiting for? Call us now and get a free quote. This way, you are not only ensured of efficient and precise rock breaking but also a commitment to safety and environmental responsibility. Take the first step and contact Liberty Demolition for all your demolition needs today.